The questions are answered by facade specialist Alamir Mohsen from Lithium Designers, Frankfurt.
GW News: How long have you been involved in developing 3D-printed facade elements?
Alamir Mohsen: The development started with academic research in 2013 and continued through a PhD program completed in 2019. Since founding Lithium Designers GmbH in 2018, we’ve transformed this innovation into a market-ready product, culminating in the world’s first building project with certified 3D-printed metal nodes in 2021.
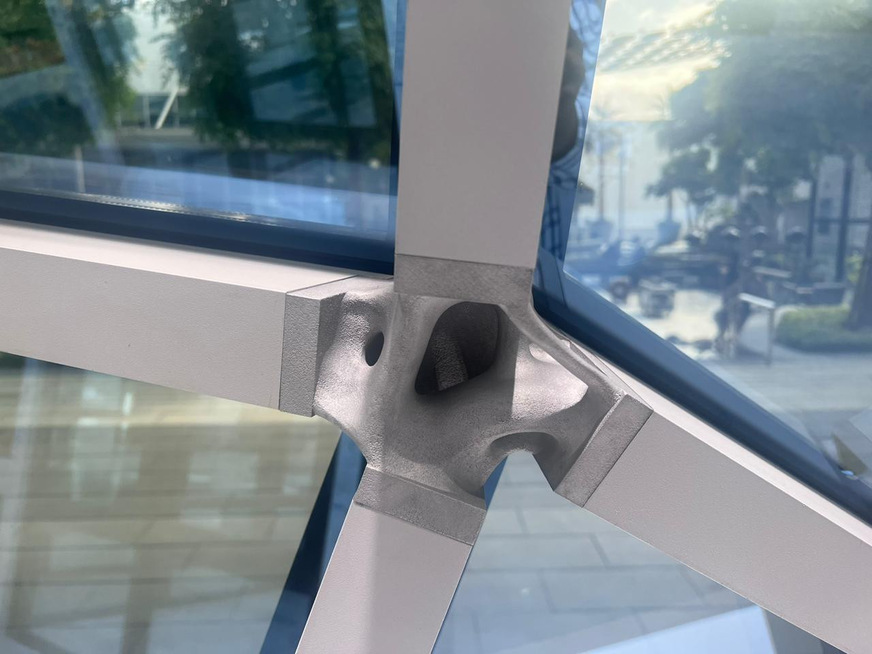
Lithium Designers GmbH
GW News: How many projects have you built using your 3D-printed nodes?
Mohsen: Our first built project with 3D-printed nodes was the award-winning HivE facade in Adelmannsfelden, where we installed 134 unique aluminum nodes using our proprietary Li3_Method. While our planning software Li3M was also used to realize the iconic 5,000 m² glass roof for the Westfield Hamburg Überseequartier, the project scale required CNC-milled nodes. However, we successfully completed our first international project using 3D-printed nodes at the end of 2024 in Saudi Arabia—an exciting milestone for us. We’re currently awaiting the official release from the client, and while we can’t share details yet, it marks a major step in proving the global scalability of our technology.
GW News: How is the development progressing?
Mohsen: Development is progressing steadily. We’ve transitioned from research to real-world implementation, completed key certifications, and are now expanding our software (Li3M) capabilities and manufacturing network. Our focus is on industrial scalability, international licensing, and supporting more systems beyond the pilot applications.
Interview conducted by gw-news.eu
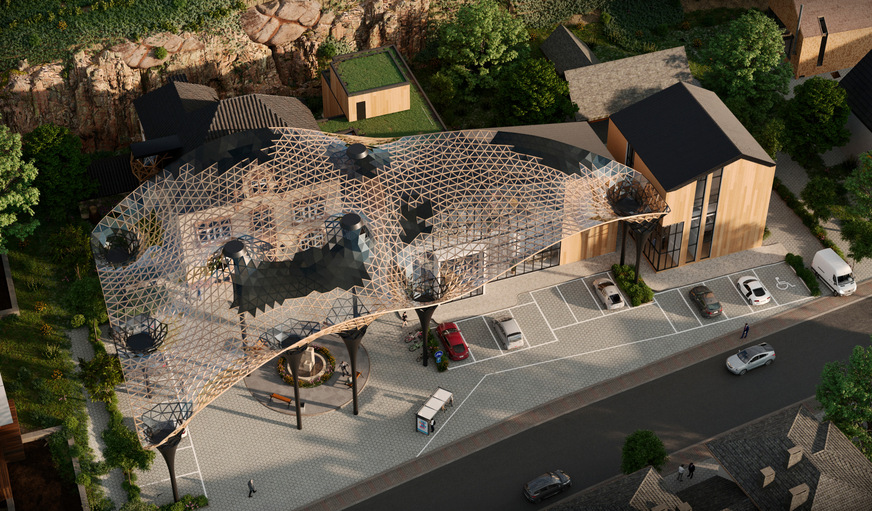
Lithium Designers GmbH