The questions are answered by facade specialist Alamir Mohsen from Lithium Designers, Frankfurt.
GW News: What makes your approach more sustainable compared to conventional facade systems?
Alamir Mohsen: Our approach reduces material waste by using only the structurally necessary volume for each node. Additive manufacturing eliminates excessive off-cuts and machining waste typical in milling or casting. Furthermore, the assembly process avoids energy-intensive welding, and the digital planning reduces coordination errors and construction time, enhancing both ecological and economic sustainability.
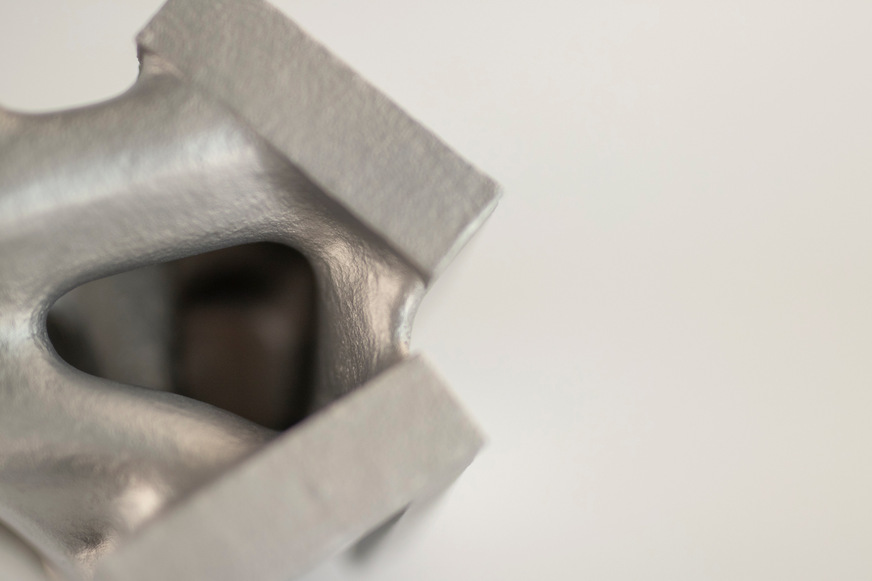
Lithium Designers GmbH
GW News: How is the 3D-printed node structurally stable compared to CNC nodes?
Mohsen: 3D-printed nodes, especially those made from SLM-processed metals, have been proven through both simulation and physical testing (e.g., at KIT) to surpass conventional construction metals in strength. The optimized design ensures better load distribution, while each node undergoes validation to meet building approval requirements, ensuring structural integrity equivalent to or greater than CNC-milled parts.
GW News: Is there any size limitation for 3D-printed nodes?
Mohsen: While current 3D printers have chamber size limitations, our nodes are designed within those constraints and, when necessary, modularized into segments. For larger nodes, we develop hybrid solutions or multiple-assembly components that maintain structural performance while staying within manufacturing parameters.
Interview conducted by gw-news.eu
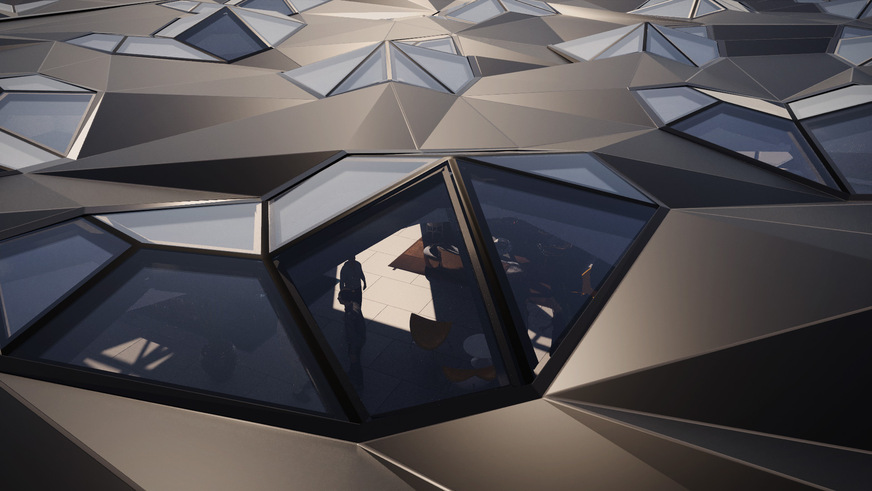
Lithium Designers GmbH