It is imperative to make sure spacer technology is effective and sustainable. In an insulating glass unit, spacers determine the width of the gap between two or more sheets of glass. The primary role of spacers is to provide a fixed gap between the layers of glass.
Over the years, the glass industry has seen many developments and changes when it comes to materials and technologies used to make insulating glass spacers. Because spacers define the amount of heat and cold that can pass through the glass panes, spacer technology is one of the key factors ensuring glass performance.
Wide variety of spacer options
Today, as demand for greener construction materials is high, ever more focus is placed on glass spacers capable of boosting the energy efficiency of insulating glass. Insulating glass spacers are available in different materials, colours and a variety of thicknesses. For an insulating glass unit, all three are essential and affect performance. For example, even a slight change in the thickness of the spacer impacts an IG unit’s conductivity characteristics. Meanwhile, the material determines the amount of heat and cold that is able to pass through the glass and, therefore, plays a big role in the unit’s energy efficiency.
When it comes to material, spacers are typically divided into two main groups – aluminium or warm edge spacers.
Aluminium spacers:
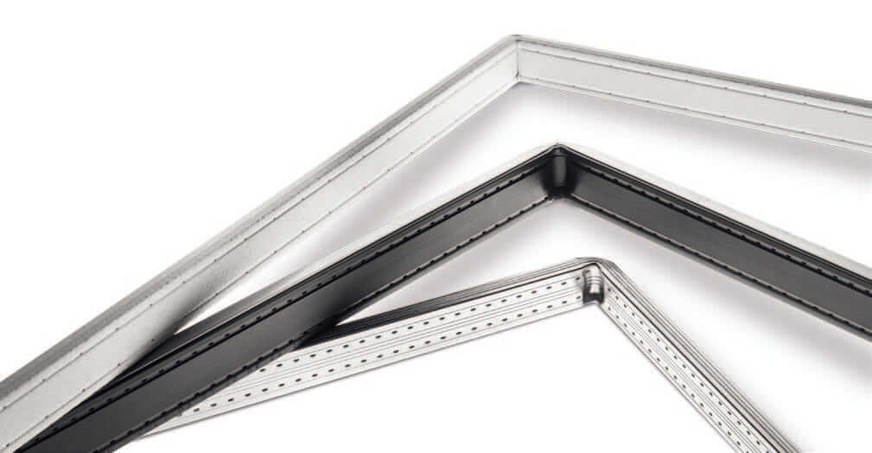
Glaston
Originally, spacers made from aluminium were the most widely used type of spacers. This material has been available for decades and provides the basic performance level.
While being a structurally strong material, aluminium is a very efficient thermal conductor. This means aluminium spacers make it easy for indoor heat to escape outside. What’s more, the cold glass edges caused by the aluminium create a temperature difference between the centre of the glass and its edges. Consequently, the insulating glass units are prone to condensation.
Warm edge spacers:
Growing energy requirements have created a demand for more innovative solutions. So, warm edge spacers made from low-conductivity materials were introduced as a higher-performance alternative to traditional aluminium spacers.
See also this Glass Basics article: Don‘t make these 6 tempering mistakes
Warm edge technology has radically changed the window market. Not only does it help prevent heat loss through windows and improve the unit’s energy efficiency, it also reduces the condensation issue.
Today, a broad variety of warm-edge spacer designs is available. Each eliminates the effect of heat loss to a certain degree while offering different levels of structural integrity.
Stainless steel warm edge spacers:
Stainless steel materials, along with their properties, are similar to those of aluminium spacers. However, stainless steel has only one-tenth the thermal conductivity of aluminium and improves condensation resistance.
Plastic-metal hybrid warm edge spacers:
Nevertheless, stainless steel spacers are many times more conductive than other warm edge spacer options. Warm edge spacers made from plastic-metal hybrid materials are typically made of plastic, such as polycarbonates, polypropylene and others, combined with low metal shims.
Flexible warm edge spacers:
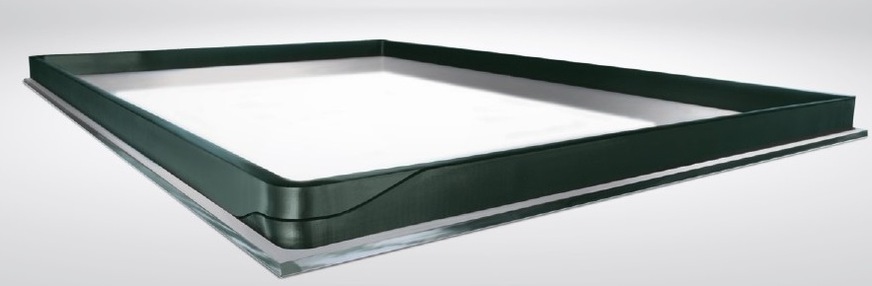
Glaston
Flexible spacers have been developed using pliable, flexible thermoplastic or silicone-based materials with incorporated molecular sieves. Among these, the hot melt butyl type of spacers without any additives stands out. And TPS is a good example.
See also this article: Study sheds light on role of spacer bars on thermal comfort
Since being originally launched in 1994, TPS technology has reshaped the insulating glass spacers market considerably. For insulating glass manufacturers, TPS provides excellent thermal insulation with many other significant advantages.
This article was published in cooperation of Glaston.
Authors: Uwe Risle of Glaston, Matthias Rehberger of Glaswelt and Malte Forstat of GW-News.
Did you know about the GW News newsletter?