Viwinco Windows & Doors, now led by Michael Duncan Jr. and Skyler Barnes, specializes in the production of windows and doors made of vinyl and offers its customers an extensive range of accessories for buildings. Customers come from both the residential and commercial sectors. “We have a philosophy to control the source as much as possible. This allows us to control quality and lead-time. The search for an innovative glass lamination process to replace an autoclave for our new glass facility led us to purchase the glass laminator - easy-Lam IFL from Bürkle," says Michael Duncan Jr.
See also: Bürkle supplies lamination line for production of solar modules
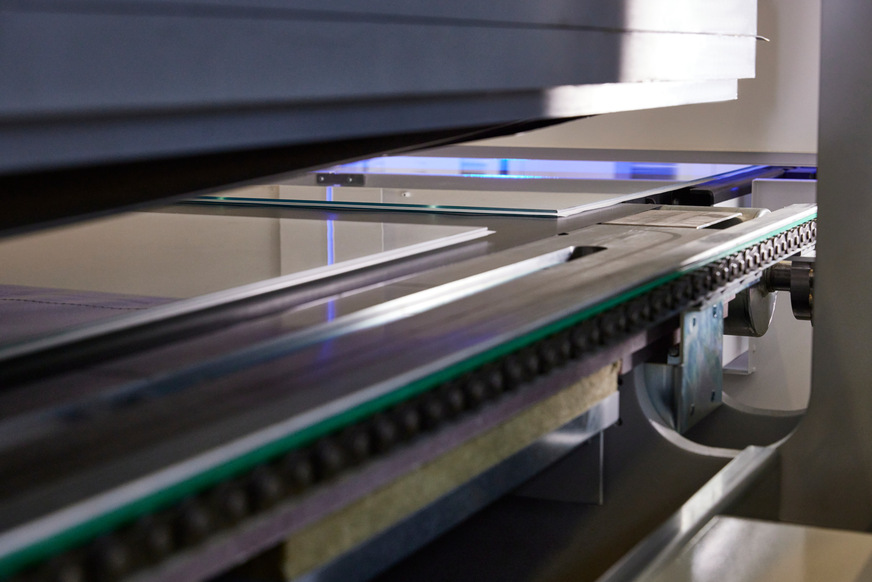
Bürkle / Viwinco Windows
Production with Bürkle's Inline Flat Lamination Process (IFL) is significantly more efficient because the pre-lamination and autoclave are no longer required. "This new technology eliminates some manual handling that can result in rejects. In addition, the laminator drastically reduces the processing time of laminated glass”, explains Daniel Klaus, Process Development Engineer at Bürkle HQ. The possibilities for saving energy were also considered when evaluating the IFL. Compared to pre-lamination and then autoclave, the energy savings of the easy-Lam IFL are around 50 percent.
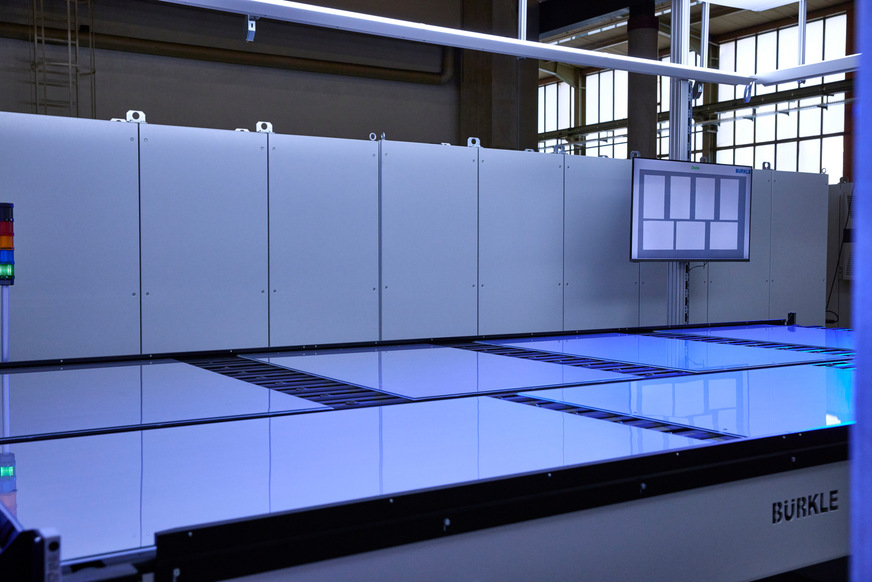
Bürkle / Viwinco Windows
In times of high energy costs, this was a convincing argument for the IFL. The laminating process with the easy-Lam IFL consists of three stages with two flatbed hot presses and one flatbed cold press. After the first stage, the glass panes are sealed and fully bonded to each other before the glass is moved to the second stage. Due to the even and individually adjustable heat application on both sides, the laminated glass can be produced to exacting standards.
More efficiency
The laminator has been successfully in use at Viwinco since the end of 2022. Impact glass is laminated there, which the supplier then installs in its window and door frames. It took around 12 months from planning and ordering to delivery of the system. “One of the most important advantages of the new Bürkle system is reducing lead time through the bed-load cycle of laminated glass every 15 minutes, instead of an autoclave system that produces a large batch every few hours. This new process aligns with our core principles of just-in-time production and smooth flow. It eliminates the waste of sorting large batches, allows us to identify potential quality issues, and turnaround remakes much quicker than an autoclave process.” explains Zach Kauffman, Operations Director at Viwinco Windows & Doors.
Also interesting: The US window market as seen by a German traveller
As the easy-Lam IFL 2650 is one of the larger systems, Viwinco can now laminate glass up to a maximum size of 2,600 x 5,000 millimeters. The smallest lite will have dimensions of 200 millimeters in width and 500 millimeters in length. In terms of glass thickness, the laminator can process packages between 2 x 0.7 millimeters and 2 x 10 millimeters in thickness. Viwinco mainly laminates glass in the thickness range of 2 x 3 and 2 x 5 millimeters.
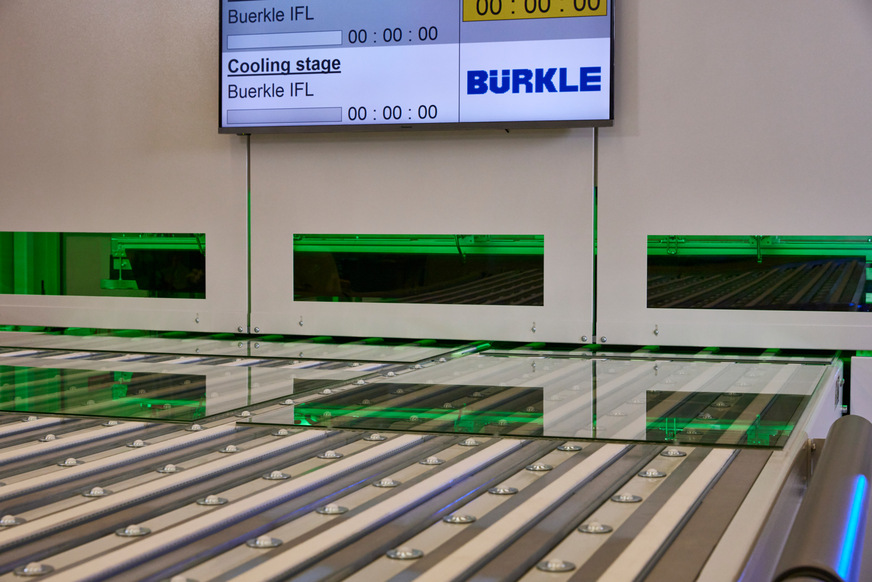
Bürkle / Viwinco Windows
The chamber height of the individual presses is 25 millimeters. As Viwinco does not produce glass of this thickness, this limitation is not a problem. According to Daniel Klaus, it is always possible to upgrade to higher chambers if required, as Bürkle has recently developed a number of new features in this area.
In order to be able to laminate glass consistently to the highest grade and quality, the installation of a clean room is a must, otherwise unwanted contamination could occur when the glass sheets are assembled.
Diverse sizes require manual trimming
At Viwinco, assembling in the cleanroom and trimming the glass sheets after lamination is done manually due to the large variation in sizes Viwinco produces. "Here in Morgantown, one batch takes between 40 and 50 minutes, from assembling to laminating and trimming the workpieces. Depending on the thickness of the glass, between 400 and 500 square meters of laminated glass sheets can be produced in a normal eight-hour shift," continues Michael Duncan Jr.
At Viwinco, around 80% of the glass is bonded with a PVB (polyvinyl butyral) foil, Sentry glass is also used when higher design pressures or larger glass sizes are needed. The glass is bonded at a temperature between 110 and 150 degrees Celsius. The laminator produces hardly any waste heat. The energy required by the two flatbed hot presses is fed directly into the product and later dissipated via the cooling press.
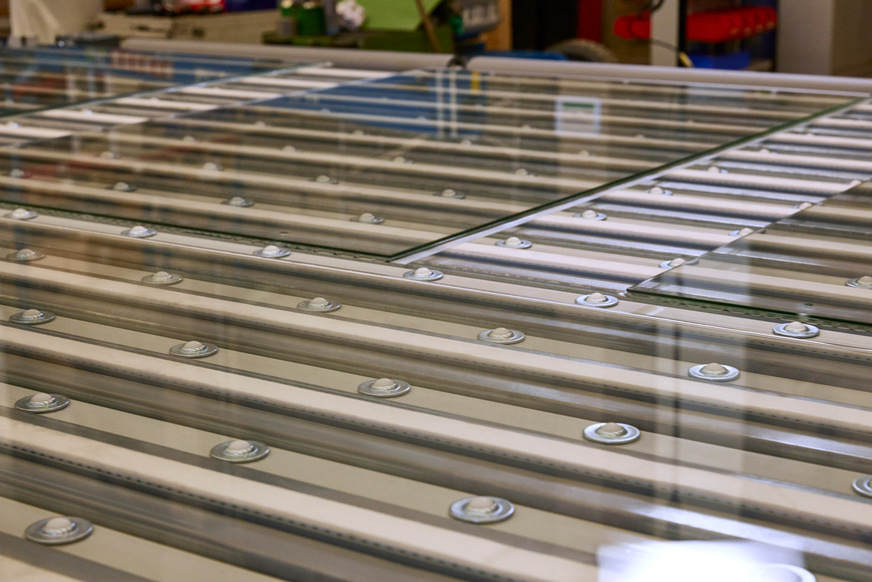
Bürkle / Viwinco Windows
High degree of automation thanks to the IFL
At the end of the lamination process, the finished glass leaves the machine at a temperature between 20 and 40 degrees Celsius. This temperature is ideal for trimming and further processing of the laminated glass.
The many manual and long processes in lamination with today's autoclaves are prone to errors and long rework times. In particular, loading and unloading of racks can cause breakage due to handling mistakes. Those problems can be eliminated with the integration of the IFL, as it can be connected directly to the existing production processes (conveyor belts). With the easy-Lam IFL, Viwinco is now able to react quickly to glass breakage or production errors thanks to short cycle times and less manual work. After 14 to 17 minutes, the next laminated batch is ready.
easy-Lam IFL was the right choice for Viwinco
The easy-Lam IFL has now been in production at Viwinco for more than a year. "The decision to undertake the project together with Bürkle and their easy-Lam IFL was absolutely right. We have been able to develop a laminated glass process more aligned with our Lean production principles, produce higher quality laminated glass, and meet our customer’s delivery needs, while reducing costs associated with the laminating glass,” says Michael Duncan Jr.
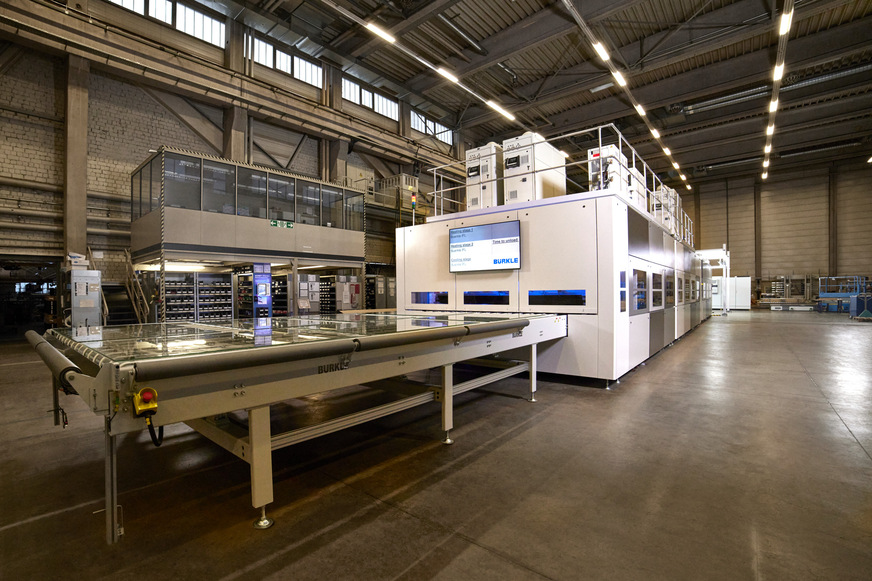
Bürkle / Viwinco Windows