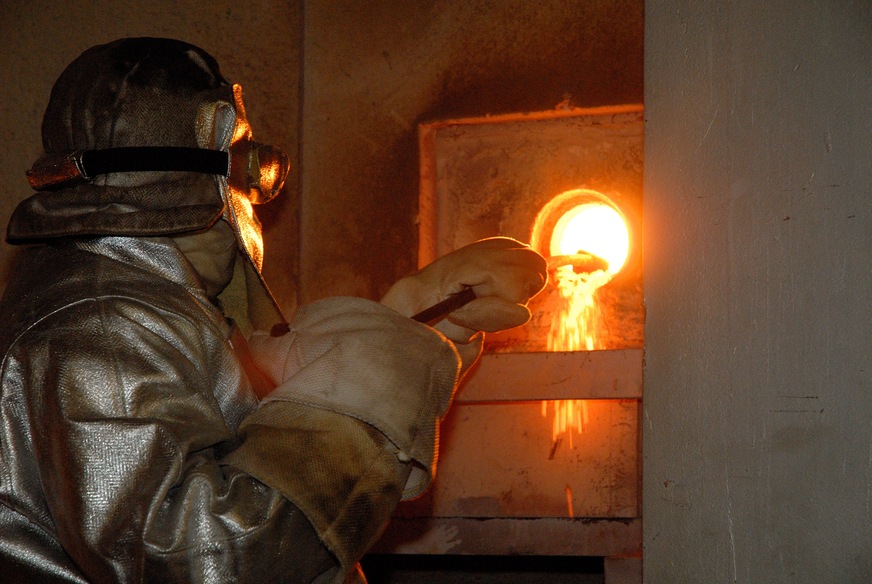
Saint-Gobain
How can the energy-intensive float glass industry so far heavily dependent on natural gas become carbon neutral by 2045? The energy efficiency of glass production is already close to what is physically-technically feasible today. Carbon neutrality can only be achieved by shifting to new key technologies and sustainable raw materials to avoid process-related emissions.
According to current surveys by the Federal Association of the German Glass Industry (Bundesverband Glasindustrie e.V. – BV Glas), up to 7.4 million tons of glass are produced annually in Germany. The final energy consumption required for this stood at 19.1 TWh in 2020, of which 15.1 TWh were generated by means of fossil fuels, especially natural gas, and the remaining 4 TWh by electricity. Every year 3.9 million tons of CO2 are emitted by systems subject to Emissions Trading, i.e. by glass melting and downstream combustion processes. An additional process-related million tons of CO2 are generated by the thermal decomposition of the carbonate raw materials.
The energy efficiency thus achieved is remarkable nonetheless: while some 100 years ago the production of one ton of glass still required 6,000 kWh, today less than 1,000 kWh suffice. While in former times approximately three tons of CO2 were emitted per ton of glass, it is less than 500 kg today. There is not a lot more to be saved here, which is why carbon neutrality requires a consistent shift to new technologies and renewable energy. According to BV Glas, the glass industry currently covers some 75% of its total energy demand by natural gas.
Carbon-neutral float glass production by 2025
In Europe float glass, for instance, is mostly produced in cross-fired regenerative furnaces where the batch is molten at constant process temperatures of around 1,650°Celsius over the complete life of the furnace, ideally at least 15 – 20 years.
Many of the major glass producers and associations are already conducting in-depth studies into sustainable transformation options, such as Saint-Gobain, for instance. This company is currently examining and will still be until 2025, how its production at the Herzogenrath site might become carbon neutral. They see the highest potential in using regeneratively produced, green hydrogen for glass manufacturing. Energy savings could still be achieved in processing as well as by energetically optimised energy use and supply at the site.
The project is being modelled in cooperation with the city of Herzogenrath, neighbouring communities and numerous institutes like the “Gas- und Wärme-Institut Essen e. V.” (Gas and Heat Institute), the “Institut für Technische Thermodynamik” (Institute for Technical Thermodynamics), the “Institut für Industrieofenbau und Wärmetechnik” (Department for Industrial Furnaces and Heat Engineering) as well as the “Institut für Stromerzeugung und -speicherung” (Institute for Power Generation and Storage) of RWTH Aachen. If the model test is successful, the site could be climate-neutral starting in 2030.
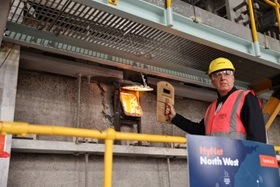
Steve Rothram
First successful float glass using green hydrogen
Another project that gives hope: last August the NSG Group Company Ltd (Pilkington Glass UK) reported the successful float glass production with the help of hydrogen as a fuel. The trial was run at Pilkington’s furnace in St. Helens (nominal load of approx. 800 tons of glass per day) in two stages: in the first stage one part of the furnace was fired with 100% hydrogen, replacing 20% of the natural gas volume in total. In the second stage hydrogen was admixed to the natural gas in all burners of the furnace. Due to the limited hydrogen supply its total share was limited to 15% in this stage of the trial.
A permanent shift could only be realised based on a comprehensive network of hydrogen pipelines – otherwise the road transport would counteract the desired climate neutrality. Pilkington’s initiative forms part of the “HyNet Industrial Fuel Switching-Project” to decarbonise industrial processes in the North-West of Great Britain.
Key technologies currently being researched
Existing manufacturing processes in the glass industry are already highly optimised to manufacture glass in a consistent quality and with low pollutant emissions. In view of the targets agreed in the Paris Climate Agreement and growing social pressure, the glass industry is doing in-depth research across its entire process chain. The option that seems obvious would be the 100% use of green power (also to avoid conversion losses), but for physical reasons not all types of glass can be molten electrically and electric furnaces are still limited in size. The furnaces usually operated in the float glass industry cannot be fully electrified at present. BV Glas estimates that it is more probable for furnaces of this size to focus on hybrid technologies that additionally rely on green hydrogen as a fuel.
[Schüco: Full carbon neutrality by 2040]
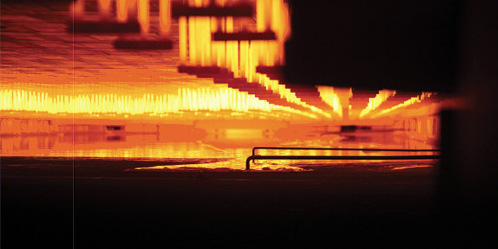
Guardian Industries
There are two key technologies on the horizon that might replace the existing base by 2045: 1. Fully electric melting furnaces that melt the batch by introducing electric energy via electrodes. The use of regenerative power alone does currently not suffice to fire bigger melting units. 2. Hybrid furnaces also using hydrogen could get up to 80% of the energy required for melting electrically via electrodes and get the remaining energy by burning hydrogen. Questions regarding the supply, availability and economic viability of green hydrogen are still unanswered at the moment.
Roadmap: Which technology is expected when?
By 2025: 100% operation of conventional melting furnaces
Late 2020s: Installation of first hybrid furnaces with hydrogen firing
From 2030:
- Shift to hybrid furnaces with hydrogen firing
- Use of fully electric melting furnaces
By 2045: Complete replacement of natural gas-fired melting furnaces
Source: BV Glas
Despite all roadmaps the aforementioned key technologies are still under research, but the possible effects in case of a successful shift can already be calculated for the float glass industry as follows according to BV Glas:
Decline in absolute CO2 emissions by 75%.
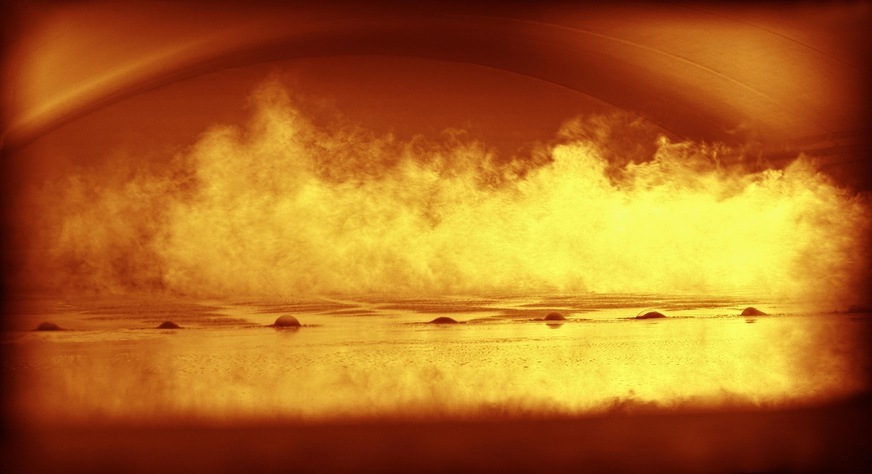
Pilkington
The share of process-related CO2 emissions from the thermal decomposition of so far non-CO2-neutral raw materials would remain unchanged. The possible use of CO2-neutral raw materials must therefore become the subject of research. The potential savings achieved by using more cullet is very limited in the float glass industry in Germany. Contrary to widespread opinion, float glass cullet in Germany is recycled almost completely, but only 11% in float glass production. The greater part is reused in the container glass and glass wool industry. BV Glas is currently preparing a publication on this topic.
The specific energy consumption decreases slightly but with an altered mix of regeneratively produced power and green hydrogen. Manufacturing costs will rise by 70% because energy costs are expected to triple compared to 2020 – the effects of the Ukraine crisis have not yet been factored into this estimate – for an assessment of the situation from the German Federal Flat Glass Association, see here. Long term the successful installation of a circular material economy that functions cradle to cradle would offer savings potentials – the buzzword here being buildings as “material banks”.
Impact on production processes and product quality
As part of the “HyGlass” project the Federal Association of the Glass Industry (BV Glas) and the Gas and Heat Institute (Gas- und Wärme-Institut Essen e.V. – GWI)) are studying the impact of using hydrogen as a fuel on the extremely sensitive process of glass production, product quality and pollutant emissions. This study includes both a view of all processes when increasing amounts of hydrogen are admixed to natural gas and the 100% use of green hydrogen along the entire glass production chain.
[Optimized production thanks to the digital twin]
The HyGlass project here focuses on studying the impact of hydrogen on regenerative melting furnaces and the downstream combustion processes, for instance in the feeders used in the container glass industry. This makes sense since the European gas industry plans to directly feed a rising percentage of hydrogen into the natural gas grid in addition to building dedicated hydrogen infrastructures in future. Then the production plants in the glass industry will also be supplied with a mix containing significant amounts of hydrogen and therefore featuring combustion properties different to natural gas – producing an impact on product quality, pollutant emissions and possibly on the plant lifecycle.
The impact of molten glass feeders on glass quality
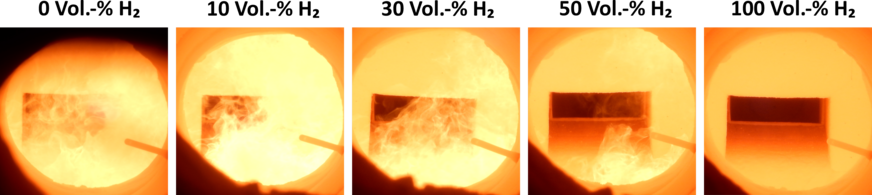
GWI Leicher, J., Islami, B., Giese, A., Görner K., Overath, J.
The impact of all this is specifically studied by HyGlass – especially in terms of combustion, which plays an important role in many process steps, in melting and in the so-called feeders which transport the molten glass and where it is homogenised for moulding. The melting process is the most energy-intensive part of glass production and the feeder is often decisive for high product quality. One anticipated difficulty here is that melting furnaces and feeders will differ substantially in technical terms and also in terms of size and energy needs.
While in the melting furnace burner systems with non-premixed flames and high air preheat temperatures or oxy-fuel burners are used, feeders use numerous small burners with premixed flames mounted to the side walls. Accordingly, the effects of higher hydrogen contents in natural gas need to be assessed differently. While with feeders, process control and possible flame flashbacks are especially relevant questions, the priority aspects for melting furnaces are efficiency, heat transmission and nitrogen oxide emissions (NOX).
Hybrid melting furnaces using hydrogen
The necessary product quality is influenced both in the feeder and in the melting furnace. Initial results of the studies indicate that the effects of hydrogen on combustion are manageable but that previously fine-adjusted measuring and control technologies are required. The thermal nitrogen oxide emissions (NOX) can rise with a higher hydrogen content, but the proven measures for NOX reduction should continue working once adapted.
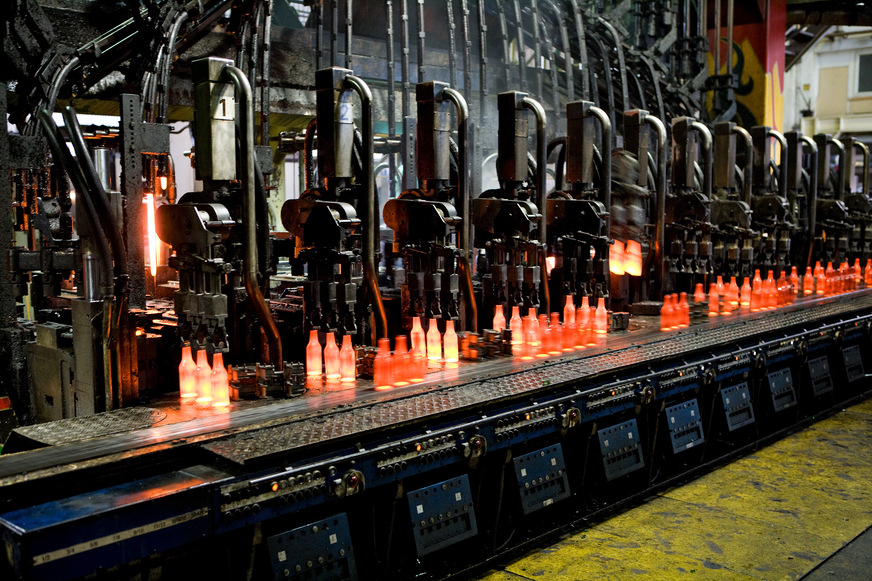
BV Glas e.V.
In the light of these studies it would make sense to bring these two key technologies – fully electric and hybrid melting furnaces with hydrogen – to market maturity as soon as possible – in cooperation with the plant and component manufacturers already operating in Germany and Europe whose expertise should be incorporated into a national strategy.
A global challenge is our consistent departure from fossil energies and the speedy installation of infrastructure for regenerative power along with the connection of glass industry sites to a hydrogen infrastructure yet to be created. Here political foresight and planning are also an imperative – also in view of the long investment cycles. To achieve full carbon neutrality plenty of research in sustainable raw materials is still needed in addition to this and the creation of a reliable circular economy.