The good news first: The digitalization process can start at any point in the value chain in new or existing glass plants. Making a start will then open up fresh perspectives on a comprehensive approach that incorporates product design, process and plant design, engineering and commissioning, operation, and services. Understanding in detail how the virtual and real worlds complement each other makes it easy to appreciate the prospective benefits of a fully digital company where all business processes are integrated and digitalized. The underlying principle is an integrated concept of the much-vaunted digital twin, which takes three forms: the digital twins of the product, production, and performance. In the glass industry, this specifically involves digital twins of product, process, and plant design, a digital twin covering all aspects of engineering and commissioning, and a digital twin for ongoing glass production.
The digital twin helps glass manufacturers, machine builders, and plant manufacturers to use the right infrastructure (hardware, software, communication, security, services) to establish a self-contained link between virtual and real production. Using this link, they can optimize virtual production using the performance digital twin of the real production process. When the simulation process has been completed and these optimization scenarios have been put into practice, the cycle starts over. “The goal is a closed circuit that connects the virtual world of product development and production planning with the physical world of production system performance and product performance,” explains Tobias Wachtmann, Head of Vertical Glass & Solar at Siemens since June.
How the digital twin grows, step by step
At greenfield plants, virtual production begins in the stage of process and plant design – in other words, when the focus is on designing, simulating, and engineering the process plant. A digital twin of the plant, including its automation systems, is generated automatically building from collaborative platforms and with full data integration from design to engineering and commissioning. The digital twin can then be used in real production with minimal effort, saving engineering costs and reducing the time to actual commissioning. The same applies to machine design, which means that machine builders can support glass manufacturers with digital twins both in the early stages and later, during virtual commissioning and in ongoing operation.
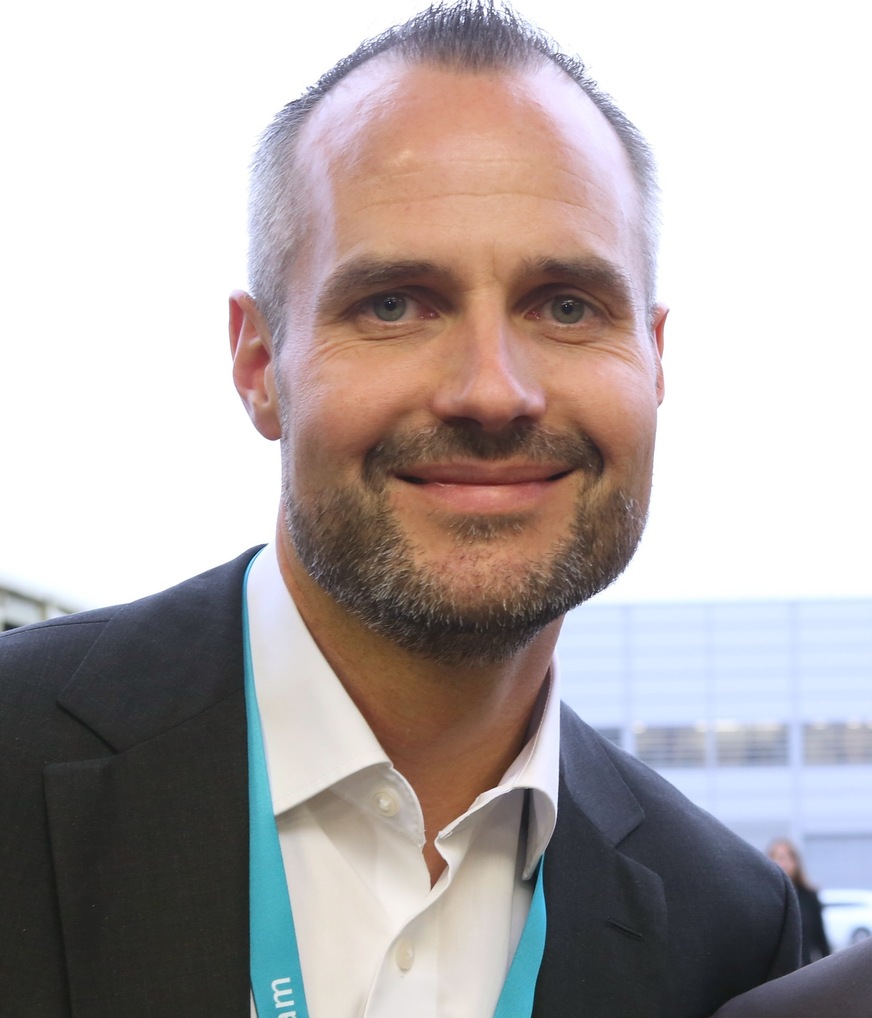
Siemens
With digital twins, you can also develop better glass products in a much shorter timeframe. The digital twin makes the design process more efficient, because it can be run and tested with more configurations than would be physically possible in real time.
In the real world, process control systems and manufacturing operations management (MOM) ensure that production runs reliably. They also help gather relevant data in order to generate a digital twin for performance. The performance digital twin is created on the basis of the real production systems and is enriched with IoT data. It can then be used to optimize production and maintain critical equipment.
Related article:
Balancing daylight access with solar shading
Existing plants already have hardware, software, and processes in place – in some cases, for decades. But even in these cases it’s still possible to draw on the huge benefits that digital twins offer in order to optimize existing processes and equipment. A digital twin of an existing glass plant can break down information silos and ensure that modernization and maintenance activities are performed using up-to-date documentation and relevant operational data. The result is a significant reduction in search times and errors. Once the digital twin has been generated, integrated workflows can be used to keep it up to date for the remaining service life of the plant – creating a permanent closed circuit between the virtual and real production systems. The simulation of optimization scenarios, for instance, can help glass plant operators optimize plant performance and seamlessly integrate their supply chains in conjunction with the integrated collaboration platform.
Practical integration of future technologies
“Although we can now provide a clear description of how the virtual and the real can be profitably combined, a number of managers would justifiably welcome guidance from established experts, especially since new technologies are appearing at a very fast pace,” says Wachtmann, alluding to the proven Digitalization Consulting services offered by Siemens. “Our teams bring together industry-specific knowledge, from raw materials to the finished product, with expertise at the field, automation, process, and company management levels and in the associated IT requirements. The result of the consulting process is a digitalization roadmap that takes account of specific requirements, business models, and existing infrastructure (IT and OT) and examines and assesses them.” The digital transformation can then unfold based on planning laid out in the roadmap – which also includes ROI calculations in addition to the digitalization measures defined. “The result is a transformation to a company that operates digitally – a transformation which the glass company itself can carry out,” Wachtmann continues. “For our part, we offer an integrated portfolio of customized solutions comprising hardware, software, communications, security, and services.”
Related article:
Sliding windows provide scenic panorama
A technology that’s currently being talked about a lot – and not just in the consulting process – is Edge computing. Cloud or Edge? Thanks to Industrial Edge, this question is no longer relevant. With Industrial Edge, you’ll enjoy all the benefits of Edge and cloud computing – optimally tailored to your company’s specific requirements. Industrial Edge allows you to analyze all data at the machine or pre-process it instantly. The optimized data points can then be transferred more efficiently to a cloud-based, open IoT operating system, like MindSphere, where you have access to more computing power and larger storage capacities. Among other things, this enables a precise analysis of data over longer periods of time.
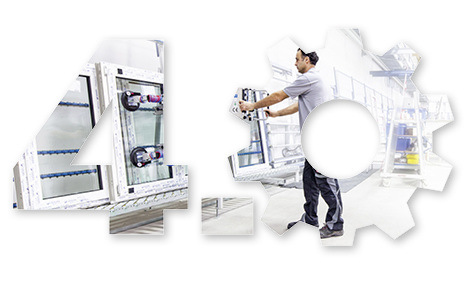
A+W
“Artificial intelligence is also an important design feature in the future of automation in the glass industry,” Wachtmann affirms. “Scalable solutions from the field level to the controller and the edge level all the way to the cloud will be feasible in the future. This means that an AI solution can be adapted to its environment and target application as needed, either at the machine or for solutions across all machines or even plants. Production processes for downstream glass users will also be fully automated in the years to come. This will mean a boost in transparency and efficiency at all levels.”
The bigger picture
We know that the whole is greater than the sum of its parts. Only a smart combination of hardware, software, and services results in Industry 4.0, the frequently invoked digital transformation of industrial processes. The drivers of this development include all the fields of technology described and those still to come – as well as the companies that have a well-thought-out plan.