Alastair Pilkington developed the float glass process in a way that it could be used industrially and presented it to the public on 20 January 1959. In 1966, the Pilkington Brothers company in St. Helens (Great Britain) began production and subsequently granted a large number of licences to other flat glass manufacturers.
The new process almost completely replaced the previous flat glass production methods of casting or blowing. Soon most of the world's flat glass came from float glass plants. Transparent and flat glass has since become significantly more inexpensive and is now a versatile building material used on a large scale in architecture. This allowed also to expand the use glass in facades and buildings as never before.
What is float glass?
Float glass is flat glass that is produced in the float process. This is an ‘endless’ process in which the molten glass is continuously fed from one direction onto a bath of liquid tin. The glass then floats on this bath. This process is now used to produce about 95 per cent of all flat glass in all areas of application, such as insulating window glass, car windows and mirrors.
Did you know? Guardian Glass launches new float line in Poland
According to DIN 1249 (flat glass in construction) and DIN 1259 (glass), the term plate glass refers to flat and transparent glass. Now it is often used as a synonym for float glass. Since it serves as the basis for flat glass in almost all areas, float glass is often also referred to as basic glass.
How does the float glass process work?
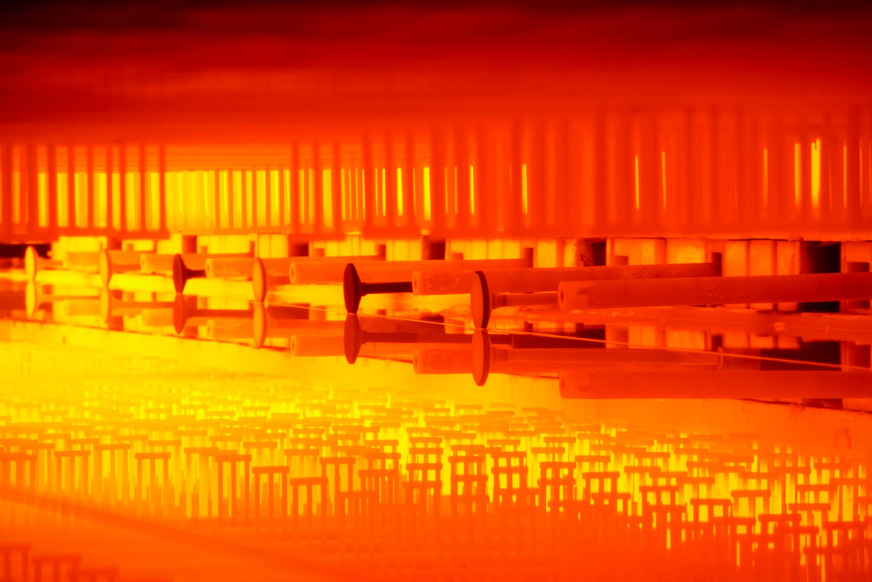
Pilkington
Float glass production is a never-ending, continuous process. The pure, refined molten glass, which is doughy and liquid at 1100 °C, is continuously fed from one side onto an elongated bath of liquid tin, which at around 230 °C is much cooler. Because glass has about a two-thirds lower density than liquid tin, it floats and spreads evenly like a film. The surface tension of the liquid tin and the molten glass creates very smooth surfaces.
The float glass, which has solidified at the cooler end of the bath and still has a temperature of around 600 °C, is continuously pulled out and passes through an annealing furnace where it is cooled down without tensioning. After a visual quality inspection, the glass is now cut and sent on to processors and finishers as basic glass. The standard size of a 'raw' float glass pane in Europe is 6000 × 3210 mm. But a glass length of 20 metres and more is possible.
A float glass plant runs non-stop for 11 to 15 years, 365 days a year, around the clock (tub travel). After that, a cold overhaul is required, during which the tub lining is renewed. To illustrate: A larger float glass plant produces about 3000 square metres of glass at a thickness of 4 millimetres per hour, which corresponds to a yearly output of about 290.000 tonnes.
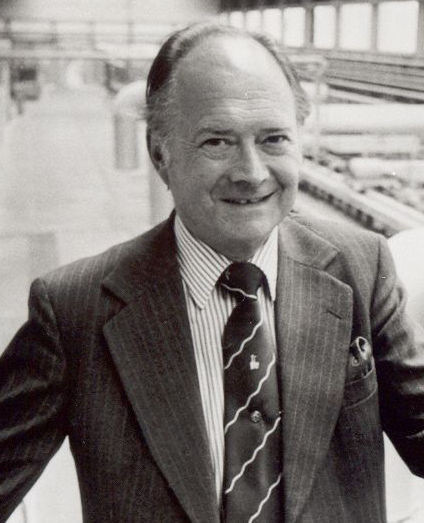
Pilkington
How was the float glass process invented?
As early as the middle of the 19th century, Henry Bessemer had the idea of using liquid tin as a medium for floating flat glass. In 1902, William E. Heal was granted a patent in the US for the manufacturing principle of running glass continuously over a tin bath to obtain plane-parallel surfaces. This patent was never used commercially.
In the late 1950s Alastair Pilkington developed the float glass process further for the industrial use and changed glass making forever.
Did you know about the GW News newsletter?