Read the article here: SentryGlas celebrates 25th years of making glass panes stronger
GW-News - What were the substantial milestones in the 25-year history of SentryGlas?
Troska - SentryGlas was originally developed as a solution for hurricane requirements. It is now also used wherever a high residual load-bearing capacity is required (e.g. in the Skywalk in the Grand Canyon/US), or high structural rigidity. Due to the coupling effect, glass panes with SentryGlas as an interlayer can be made thinner than with PVB interlayers.
Has your customer structure changed over the last 25 years?
Yes, and in a substantial way! In the past, we only had contacts with fabricators and provided technical advice. Today, we maintain intensive contact with planners. We are therefore very close to the designs and don't have to wait until the realisation stage. This means we can provide valuable assistance right from the planning stage. Also with our apps, such as the "Strength Lab AI". This tool allows you to quickly analyse practically all glass configurations, dimensions and load cases. In addition, standard modules and load cases, which are issued in accordance with the current ASTM, EN and DIN standards, make it easy to analyse the results.
Will intermediate layers perhaps become superfluous because the functions can be integrated into the glass itself at some point?
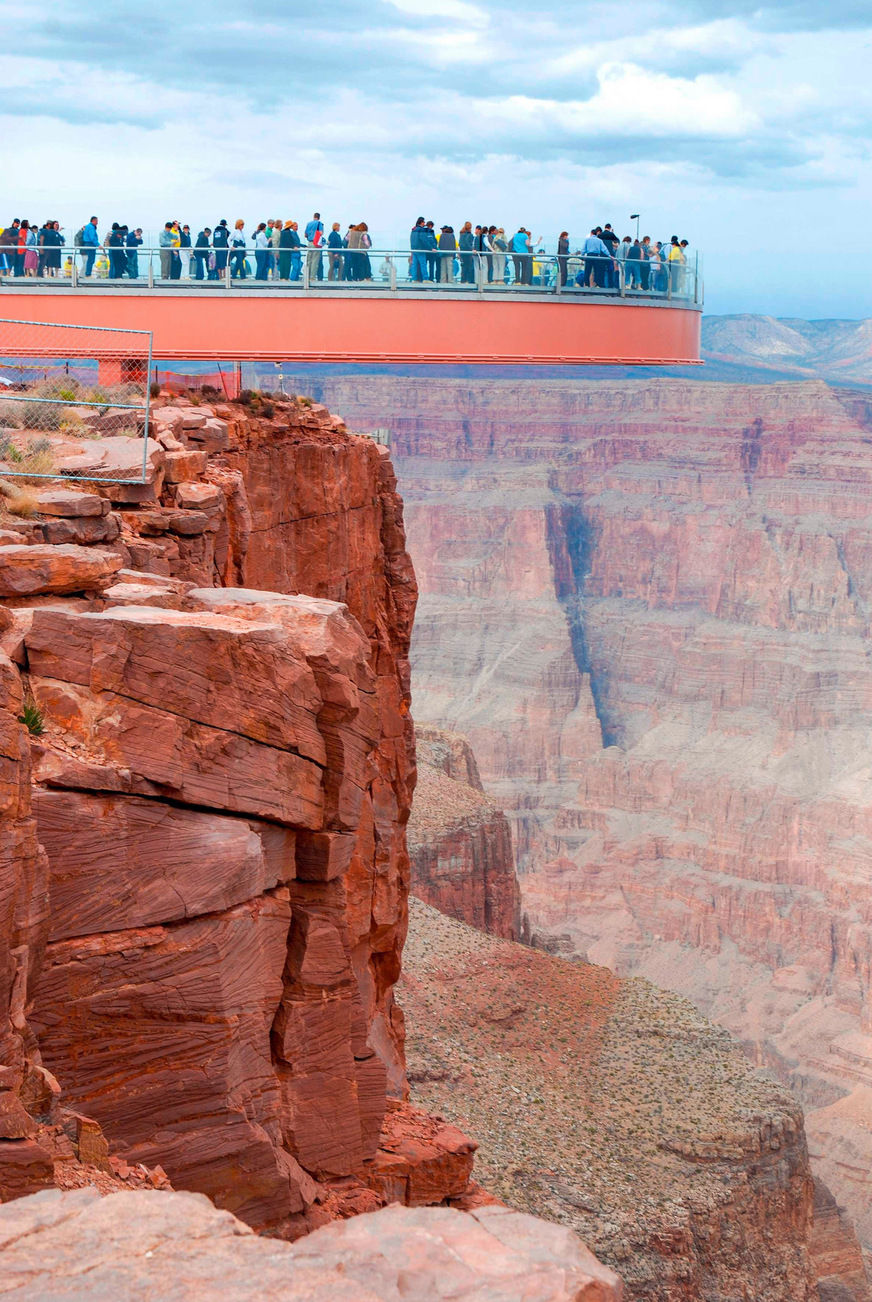
Grand Canyon West
I don't think so. The films give the glass a property that the glass alone cannot achieve. Glass is a brittle and fragile material that does not simply become elastic and tear-resistant. I think that many of the functions that are painstakingly applied to glass today could be replaced by film in the future. Another topic that will become increasingly important in the coming years is the sustainability of products, I think. It starts with the carbon footprint and ends with the issue of recyclability. In terms of carbon footprint, we are already very good compared to our competitors. We have EPDs for our Trosifol PVB products and also for our SentryGlas. The coupling effect I just mentioned allows us to make the glass thinner, especially for SentryGlas.
Can you please give us a few examples?
Around 3 kg CO2/m² glass and mm glass thickness are emitted during the production of conventional float glass. If, for example, you replace a 16 mm LSG with Trosifol UltraClear with a 12 mm LSG with SentryGlas, you save 12 kg of CO2 on the glass and an additional 1 kg of CO2 on the interlayer.
Also interesting: Coated glass from Guardian and interlayers from SentryGlas certified for France
Or take screen-printed glass, which is not recyclable. In future, glass printing could be replaced by printed PVB or SentryGlas. And coated glass corrodes over the lifetime of an insulating glass unit. Although it can be remelted, it cannot be directly recycled (no re-use). If the coating were to be applied to a film instead, only the film would need to be replaced. We will see many new developments in films in the future.