Since the beginning of the year, the East End Gateway, a 12-metre-high letter A, has been guiding travellers from 33rd Street via escalators to the underground platforms of New York's Penn Station. The filigree cable net façade not only sets an architectural accent at one of the largest railway stations in the USA, but is also equipped with state-of-the-art monitoring technology.
At normal times, 650,000 people visit the junction at the famous Madison Square Garden every day. In order to equalise the flow of people, the client MTA C&D (Metropolitan Transportation Authority Construction & Development) together with Vornado Realty Trust commissioned the construction of a new, spacious main entrance. The result is a filigree structure made of steel frames and stainless steel cables, which supports a highly transparent shell of glass to direct as much light as possible into the interior.
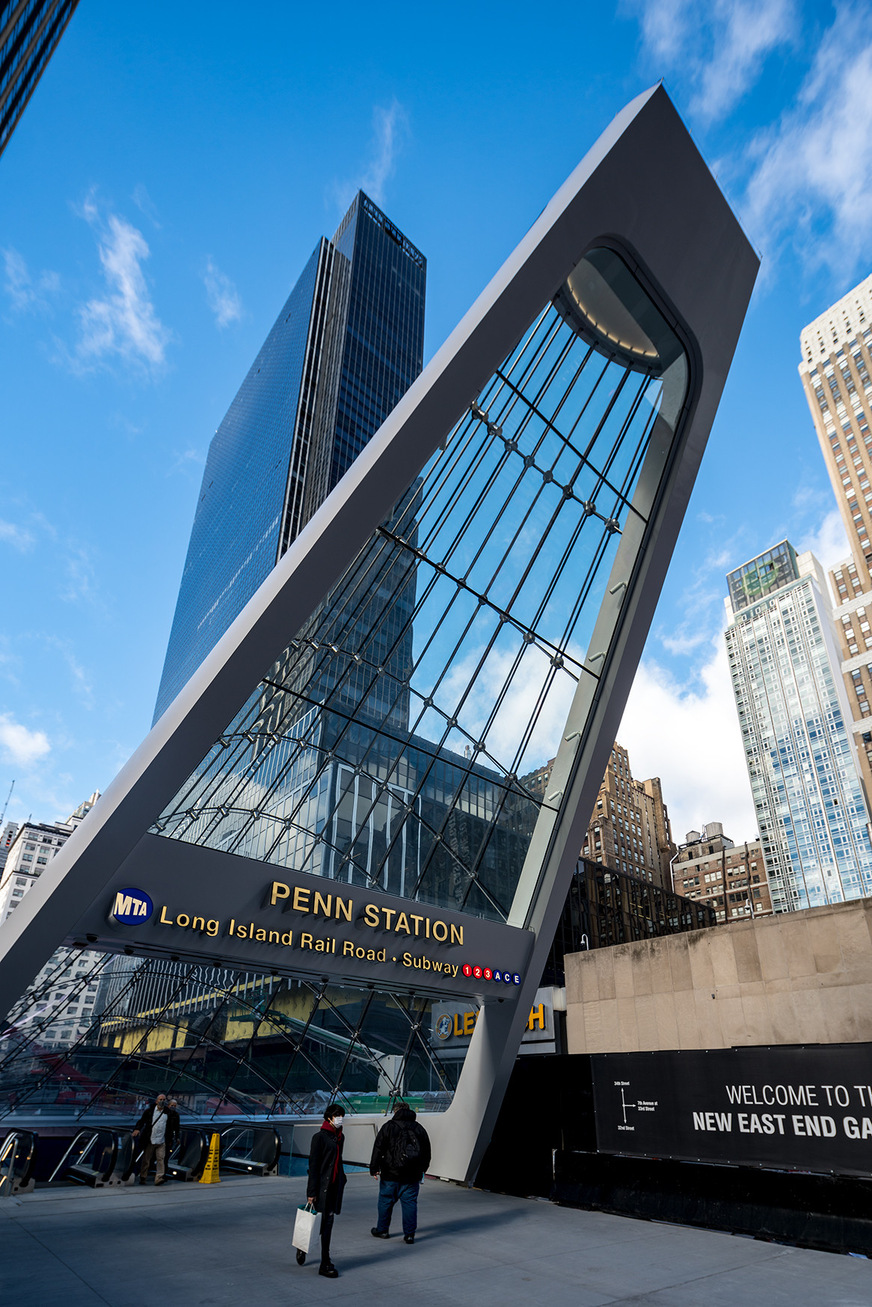
Field Condition
The design continues in the opening to the basement: 60 double-curved and linear panels of black steel suspended from a substructure form the cladding of the oval opening. The funnel-shaped form creates a flowing transition upwards to the canopy, resulting in a seemingly infinite perspective. The glass roof also provides the ascending travellers with an unobstructed view of the Empire State Building.
What does the ‘Horseshoe’ do in seele's construction?
The rope facade designed by seele consists of a steel frame with a rope net made of stainless-steel transverse and longitudinal ropes braced against each other. The facade specialist planned a 14.6 metre high, A-shaped steel frame as the primary supporting structure.
The floor connection is formed by the so-called "Horseshoe", a horseshoe-shaped edge beam with a length of approximately 30 metres and a width of 13 metres. The complete steel structure consists of five welded box girders, a cross girder and the so-called ‘crown’ - a solid piece of 400-millimetre-thick sheet metal placed on top of the structure. Attached to this crown are rope attachments for the facade as well as the tensioning fixtures. A total of 105 tons of steel was machined for the frame structure.
What requirements were there on the welding joints?
The entire steel structure is out in the open and constantly exposed to the elements, so surfaces and welds required high-precision machining and needed to comply with American AESS 4 requirements.
In order to achieve the inclination of the entrance envisaged in the design, the A-shaped frame was built in an over-slung manner and tilted to the required 45-degree angle by the cable tension, thus achieving the total height of 12 metres.
Here is another impressive seele project: Famous ship‘s hull beautifully encased in glass
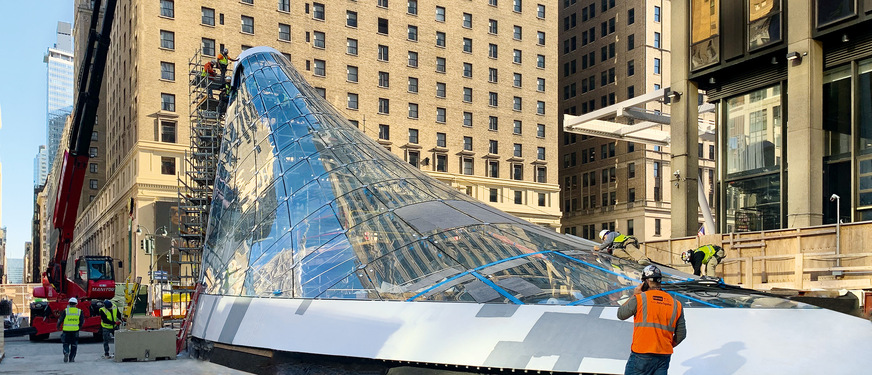
seele
To enable a smooth assembly in New York, the steel construction was completely assembled and tested for a preliminary test in the Czech Republic at seele in Pilsen and then shipped to New York for final assembly by seele and Skanska USA Civil NE.
Assembly in the tightest of spaces, in the middle of Manhattan, required skilful coordination of the assembly. The individual components were delivered just-in-time. Within three weeks, seele assembled the massive steel structure. The individual cables were then attached, extended with adapter pieces and then tensioned to give the frame its final shape. Then came the glazing.
How many double-curved glass panes did seele use in the facade?
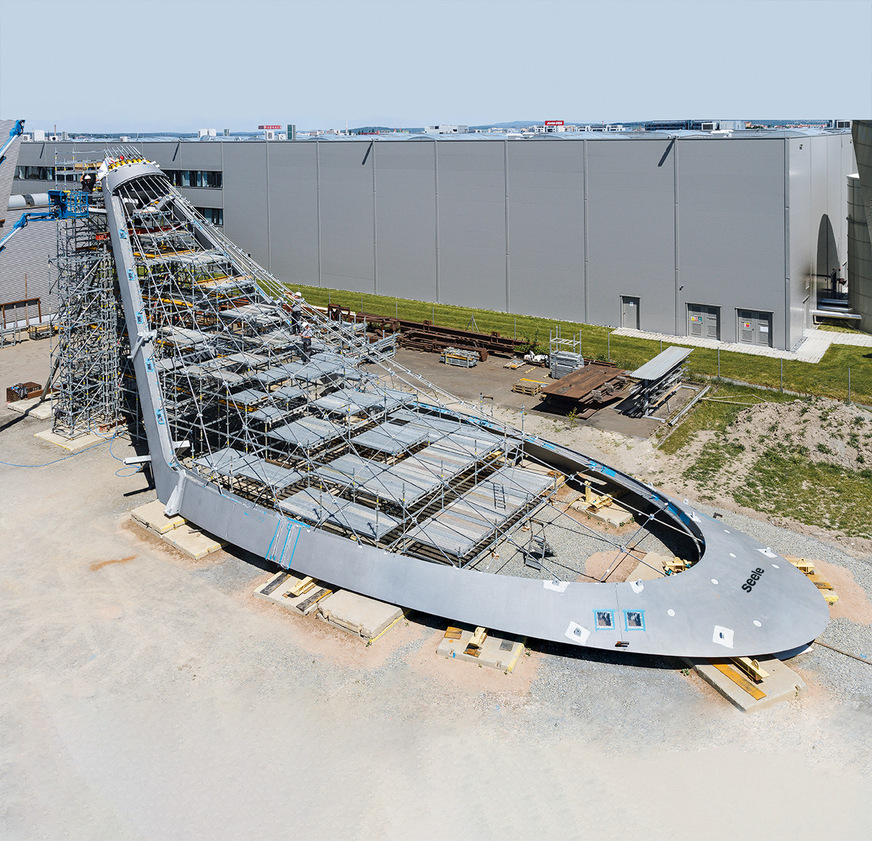
seele / GONO / Petr Nový
Almost 140 double-curved glass panes were transported from Europe to New York to the construction site and fixed in the cable net with special brackets. Each laminate is unique, because the SGP interlayers are printed with different dot patterns. In November 2020, the call was "All in!" when the last glass pane was mounted in the cable structure.
What does ‘digital facade monitoring’ mean?
The monitoring concept developed by seele is also sophisticated. The required cable force measurement was implemented by seele as a cloud-based solution. Various factors, such as small distances between the rope nodes as well as the difficult accessibility at the heavily frequented Penn Station, made conventional rope force measurement almost impossible for this project. During installation, invisibly mounted measuring points collected data on the pre-tensioning of the longitudinal and transverse ropes. This saved time-consuming on-site measurements, which can also be carried out in the future if necessary.
See also this article: Largest all-glass roof for Canada
The new entrance at 33rd Street was opened on 31 December 2020 under the name East End Gateway. The opening of the Moynihan Train Hall, Penn Station, followed just one day later. Here too, seele was involved and responsible for the execution of the over 5000 square metres of steel and glass roof structure.
The A-frame (4 panes) and the "Crown" (1 pane) were fitted with flat laminated safety glass, this was made by sedak.
The double-curved glass panes come from sunglass industry and were gravitationally bent. They are chemically hardened. The outermost SGP interlayers have been printed with a dot grid.
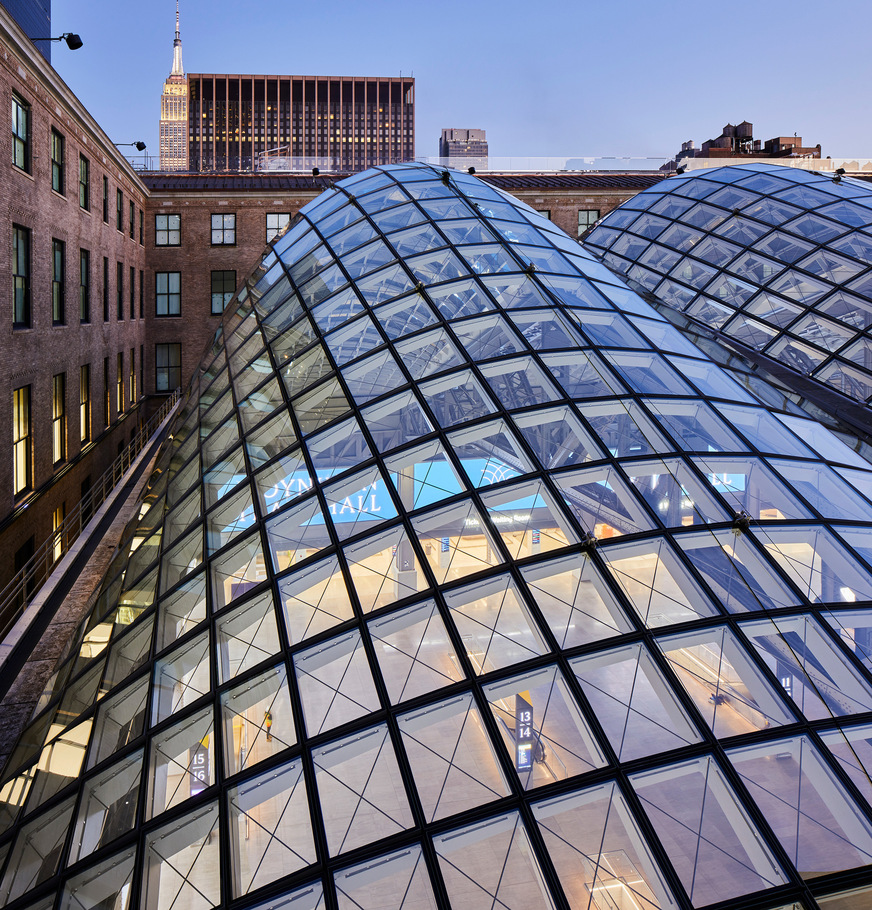
SOM
Did you know about the GW News newsletter?