GW News - After more than 30 years at Technoform, you are an expert in all things warm edge. What are the main arguments in favour of warm edge spacers?
Jörg Lenz - If you want to meet the increasing demands on the energy performance of insulating glass units, there is no getting around warm edge. This applies equally to end users, planners and insulating glass manufacturers who have to supply corresponding glass products. In terms of energy efficiency, warm edge systems are now state of the art after more than 20 years on the market, with a market share of over 70%. However, this also means that many insulating glass units are still manufactured and installed with metal spacers.
GW News - Why do building owners still rely on metal spacers?
Lenz - On the consumer side, this certainly has to do with the fact that the traditional glass edge seal with spacers made of aluminium or stainless steel is somewhat cheaper to purchase than the warm edge. The fact that the warm edge saves costs in the long run is often overlooked under short-term pressure to save money; a lot of educational work needs to be done here. In order for warm edge systems to become more widespread, everyone involved, from the planner to the window manufacturer to the insulating glass manufacturer, must pull together.
GW News - Do you confidence in this case?
Lenz - Yes. The awareness of quality is fortunately growing, but it comes up against limits when it comes to economic efficiency in production and processing. There is no doubt about it: insulating glass manufacturers must be able to produce efficiently in order to participate in the "warm edge" joint project.
A manufacturer who has always processed spacers made of metal will consider very carefully whether and how it will pay off for him to switch to hybrid spacers made of plastic and metal foil. Furthermore: Without productivity, there is no warm edge, which is why the topic of productivity is so important to me. Our goal at Technoform is to support our partners with our experience and know-how.
GW News - Is there one warm-edge system for all requirements? And what are the differences between the various systems?
Lenz - When selecting the right system, a number of factors are relevant for the insulating glass manufacturer. That is why there are different systems. To simplify, one can distinguish between two types of warm-edge systems: On the one hand, there are the "flexible", one could also call them the "soft" systems, where the spacer is applied directly to the glass panes from a roll or from a barrel. On the other hand, there are the "rigid" systems, such as the hollow chamber profiles from Technoform. These are almost identical to common metal spacers, except that they are made of thermal plastic with a metal foil as a diffusion barrier against moisture penetration into the gas gap and against loss of noble gases. They are also much more energy efficient.
GW News - What are the distinguishing features of "flexible" spacer systems?
Lenz - "Flexible" systems have the advantage that machine processing can be automated very well. The panes pass through the process almost without manual support. This saves manual effort and increases the production speed, but the IG manufacturer needs additional machines and processes for this. Warm edge systems with rigid profiles, on the other hand, can be produced with common machines and processes for processing metal spacers. In addition, profile bars made of plastic are very resistant to bending and thus stabilise the edge seal.
See also: What you need to know about insulating glass spacers
Both types of warm edge systems have their advantages and disadvantages, depending on the objective. There is no one system for all requirements, which is why large insulating glass manufacturers in particular operate on two or more tracks. The goal should always be to create the highest quality for the end user; this should be followed by questions of productivity, and not vice versa. Which technology is strategically the right one in each individual case has to be determined on an case-by-case basis. Here, too, the experts at Technoform are happy to provide support with a great deal of experience and know-how.
GW News - When you say that warm edge spacers made of plastic are a "safe bet" for manufacturers who previously processed metal spacers, what do you mean by that?
Lenz - Before warm-edge spacers came onto the market, insulating glass was manufactured with metal spacers. The metal profiles were cut to size, bent, filled with desiccant and applied to the pane in the manufacturing process, and the edge seal was finally sealed.
Most insulating glass manufacturers have mastered this process for decades. Since the same process also applies to Technoform's hollow chamber profiles, it is very easy for them to convert to plastic profiles. The producers stay on the safe side because they do not have to purchase new machines and equipment or retrain employees.
It hardly makes a difference in production whether spacers are made of metal or plastic, which is why warm edge spacers made of plastic and metal foil are a safe bet for manufacturers and a ticket to the future, because the signs of the times are clearly pointing to warm edge.
GW News - What additional services do you offer for IG manufacturers?
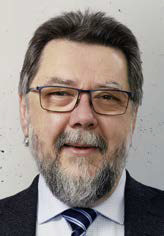
Technoform
Lenz - We support our insulating glass customers on site with the adaptation of bending systems and advise them if new machine parts have to be purchased in individual cases. However, this all involves much less effort and cost than converting to a completely new system. In addition, we have expanded our service portfolio by providing a new online shop platform that further simplifies ordering for our customers. In addition, we offer the service of a Kanban system, which ensures a steady supply and improvements in process costs on the customer side. Due to the restrictions of the Covid pandemic, we rely on remote service for customer support, in addition to personal contact, and support our customers, for example in production, by means of various digital tools. In this way, we remain close to the customer despite the physical distance. -
The interview was conducted by Matthias Rehberger
For more articles like this one, make sure to have a look at our 2021 Glass Special.