The gas crisis triggered by the Russian invasion of Ukraine has led to exorbitant price increases in the West. This shows how vulnerable our industry is due to its dependence on fossil fuels - especially natural gas. This is especially true for the glass industry.
Stay up to date, sign up for our newsletter!
Due to the availability of cheap natural gas, almost all processes in the solar glass value chain have been converted, leading to extreme dependence. In addition, all fossil combustion processes are very harmful to the climate due to the emission of carbon dioxide.
First glass melting furnace invented in 1872
The development of fossil fuel melting furnaces began with the continuous glass melting furnace invented by Charles William Siemens of Westminster, England in 1872. The regenerative process (preheating the cold combustion air) increased the overall efficiency from ten to 25 per cent (depending on size) to as much as 50 per cent. Stoves fired with fuel and oxygen (instead of air) could actually achieve an overall efficiency of 60 per cent.
Natural gas was cheaper, but also less efficient
The use of natural gas, which used to cost on average only 30 per cent of electricity, made the process less costly, although the overall efficiency of electrically heated stoves reached up to 90 per cent. Emissions of carbon dioxide and other substances from fossil fuel firing were not an issue until a few years ago. Today's gas prices, however, are higher than those for electricity.
As early as 1905: the first electric furnace
Few experts know that continuous all-electric melting (AEM) is almost as old as gas-fired regenerative melting. The first electric furnace was built in 1905 according to the design of the Frenchman Sauvageon and was used for the production of window glass.
See also: How will rising energy prices impact the glass sector?
Even small electric furnaces have a thermal efficiency of 70 85 per cent. The specific energy consumption was already less than 0.9 kilowatt hours per kilogram of glass more than 100 years ago. Despite many improvements, however, electric melting has become increasingly unpopular for all mass-produced glass due to higher costs compared to widely available cheap fossil fuels.
New interest in electric melting
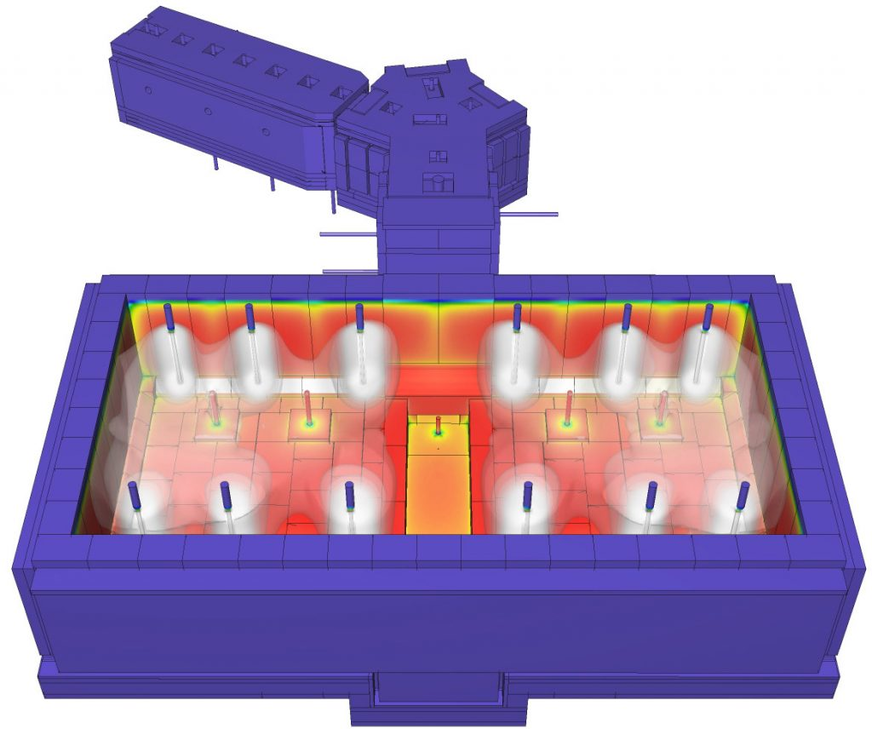
IWG Wagenbauer/Glass Service
Only the climate crisis and the pressure on the carbon footprint have rekindled interest in fully or partially (hybrid) electric melting processes. Alternative energy sources for electricity help to lower costs and reduce CO2 emissions from the combustion process in fully electric furnaces to zero.
All that remains is the CO2 contained in the batch. All electric melting furnaces can be designed and operated in a variety of ways, depending on the requirements.
Uniform and stable batch layer
Achieving a uniform and particularly stable batch layer plays a central role for solar glass. On the other hand, the batch layer should allow the passage of bubbles rising from the melt (for example carbon dioxide or sulphur dioxide).
The problem is that to achieve a stable batch layer, the drawing speed can only be varied within a very small range. If the glass drawing speed is too low, the batch layer becomes thinner. High heat losses lead to melting temperatures, so that sufficient refining to ensure high glass qualities is not achieved.
Potentially lower investment costs
As a rule, all-electric melting furnaces have a stable working window in the range of 80 to 110 per cent of the nominal capacity. In addition, electric melting (EM) furnaces have potentially lower investment costs because a smaller furnace volume is used, no regenerators are required and no expensive high-temperature vaults are needed.
In addition, combustion-related gaseous emissions (for example, carbon dioxide, nitrogen oxides and dusts) are greatly reduced, lowering investment costs for filtration systems and operating costs for cleaning.
Other advantages of electric furnaces
From an operational point of view, it is positive that less maintenance is required to clean regenerators, less volatilisation occurs (lower raw material costs) and there are lower repair costs. In addition, efficiency is not as dependent on the size and capacity of the furnace as with fossil-fuelled furnaces.
Also interesting: First architectural glass produced using hydrogen
Currently, maximum EM capacities of 250 tonnes of glass per 24 hours are possible, although this limitation cannot be explained either physically or technologically and theoretically much larger capacities should be feasible. Modular approaches are also being discussed, which seem to offer a viable solution.
250 tonnes of solar glass per day
A 250-tonne-per-day solar glass plant produces about five million square metres of solar glass (3.2 millimetres thick) per year on a net basis. This would produce solar modules with an output of about 1.25 gigawatts. The expansion targets published by the EU assume an expansion of production capacities in Europe of 30 gigawatts by 2030. In purely arithmetical terms, more than 20 solar glass production plants with 250 tonnes each per day will be needed.
Since the plants described can also be designed in a modular way, two melting tanks, for example, can be operated with a large batch preparation and the downstream refining plants. This has the advantage that different glass thicknesses (two and 3.2 millimetres) can be produced. During the cold repair that is necessary every eight to ten years, production can continue on one furnace at a time.
Solar power from the factory's surfaces
Glass production requires an immense amount of space. The site, including large areas for logistics, usually covers an area of four to five hectares. A solar power system with six to seven megawatts can be installed on this area through intelligent design with solar modules.
Did you know? Saint-Gobain managed one week of carbon-free glass production
If other traffic and storage areas in the vicinity are included, up to ten megawatts are possible. At most locations, such a solar plant will cover the entire electricity demand of on-site production, provided storage units are available. At windy locations, additional wind turbines can be installed. This results in a better consumption balance.
First pilot line in planning
In order for the vision of solar glass without emissions to become reality, Gridparity AG is working with glass technologists and investors to develop a concept for the construction of the world's first fully electric production line for solar glass. It can then be duplicated as a pilot plant in Europe.
Also by Erich Merkle: Europe threatened by massive bottleneck in solar glass