At the work shop of the processor Glass Solutions Technoglas in Emmen in the Netherlands, the Lisec glass cutting line has become outdated. It is in good mechanical condition, but it is suffering from the phenomenon called 'ageing'. Critical components of a production generation, such as PC cards, control systems, motors etc. are becoming a scarce commodity and at some time or other they can no longer be re-ordered. If one of these components becomes defective, this can therefore result in long and often costly downtimes.
When the software becomes a risk factor
Furthermore, the operating system was based on Windows 95 – meaning there was a high risk of being attacked by viruses on the one hand, and on the other hand there were few people who had the knowledge to further develop or support this system. The solution in cases such as this: Long Life from Lisec.
Emmen is about 2 hours' drive from Amsterdam. The plant was designed for the processing of flat glass and the production of insulating glass for the Glass Solutions (Saint Gobain) subsidiaries in the Netherlands, and acts as a hub: Products that are bought in from the outside are also processed via Glass Solutions Technoglas in Emmen.
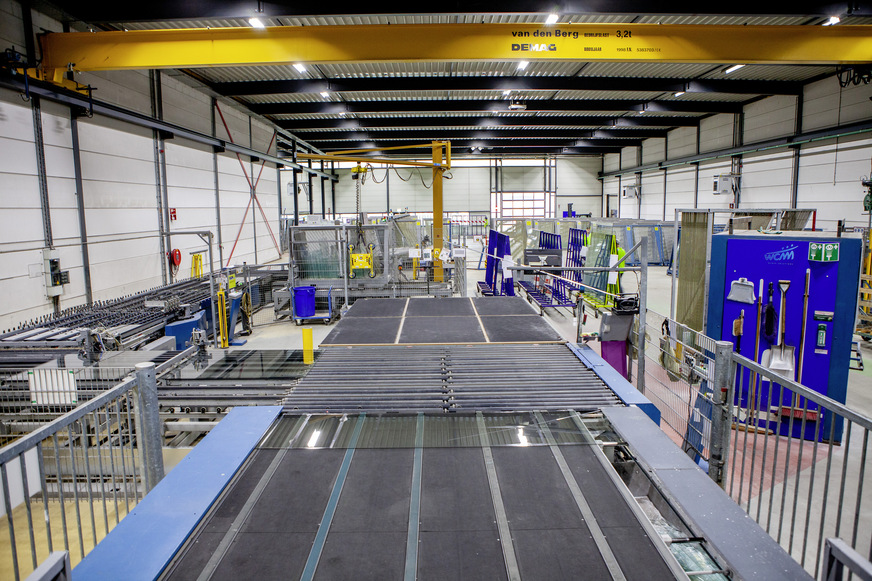
Lisec
The systems and building were perfectly coordinated with each other at the time when the system was designed – which meant the possibilities for subsequent expansions or changes were limited. The expectations are high. There is huge pressure to continue fulfilling the role of reliable partner and supplier within the group.
„We knew we had to do something – the risk was too great“
Herman Kanne, Branch Manager for Glass Solutions Technoglas: “The performance was right and we were in an ideal position. The cutting line was performing excellently, but we also knew we had to do something – the risk of failure was too great.”
In order to remain successful in the future, a project team was formed in the subsidiary, which formulated multiple options. Kanne continues: “It soon became apparent to us that a new line would be out of the question. For one thing, we were limited by the building because it was exactly coordinated with the current solution, and a new line would result in considerable building costs. Furthermore, we would also have had to consider a new logistics concept, which would have pushed the cost up even further.“
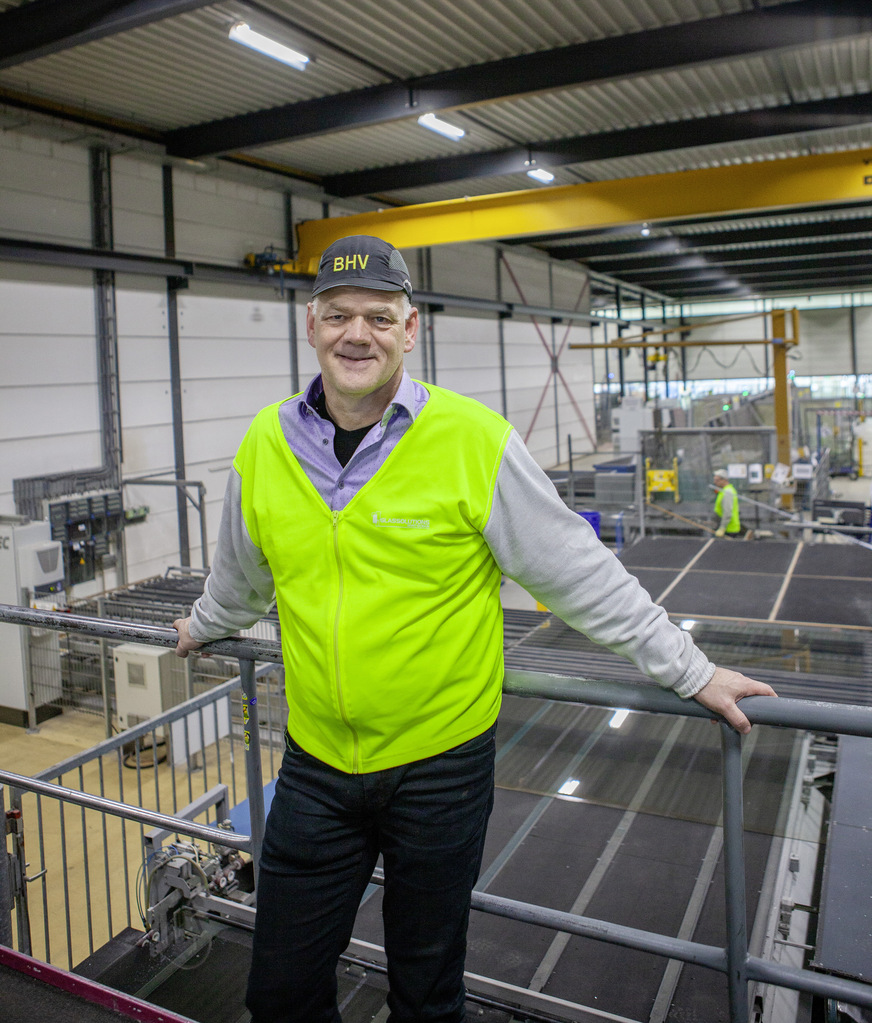
Lisec
The project also revealed that there were no alternatives on the market that performed better when it came to speed than the existing solution at the Saint Gobain subsidiary in Emmen. Branch Manager Kanne: “A sheet must be available every 7.5 seconds – that is incredibly fast, and could not be beaten by anything else that is available. This was the main reason for keeping the existing line and optimising it.”
Read in part 2 of the article next week how the management of Glass Solutions decided to optimise the existing line. Find out how they worked out a concept together with the Lisec specialists and how they made it work somoothly.