The management of Glass Solutions decided to optimise the existing line and worked out a concept together with the specialists of Lisec. Andreas Rohrweck, responsible for Long Life projects at Lisec: “The option of the Long Life approach was only feasible and made sense, because the team in Emmen had taken good care of the production line and it was in very good mechanical condition.”
New controls as key solution
Control cabinets, motors, PC cards, drives and control systems were exchanged. Particular attention was paid to the preparation of the existing sensors and actuators, in order to keep the modification work on the system to an absolute minimum and to only replace actually obsolete parts.
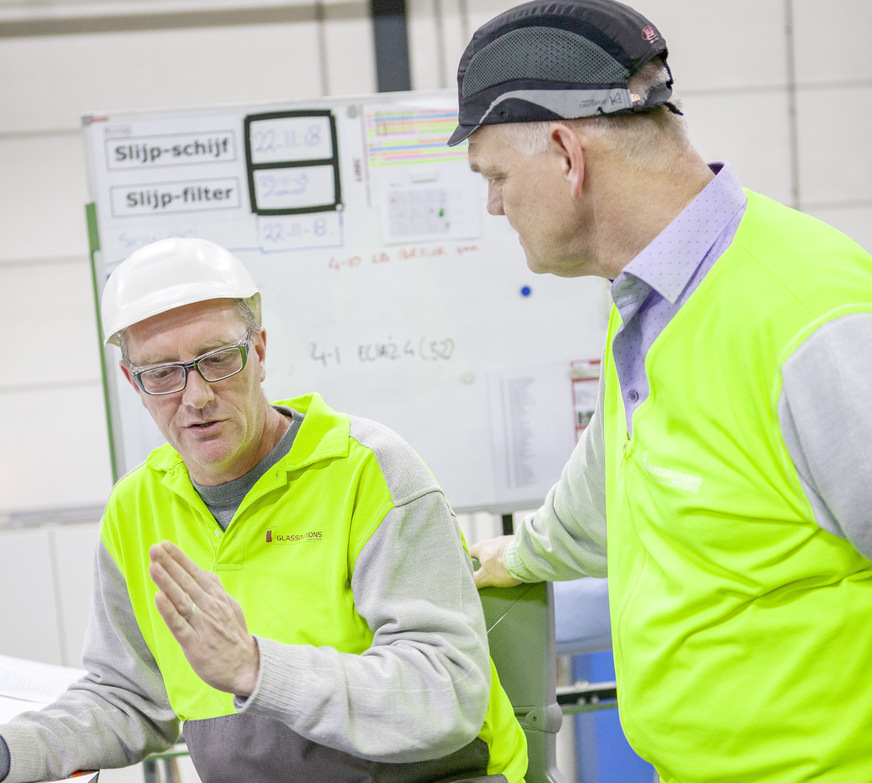
LiSEC
Herman Kanne explains: “The Long Life solution not only has the advantage of significantly lower investment costs in comparison to a new line. Another advantage is in the time needed for implementation. We were able to refit the line during periods in which servicing and maintenance work was being carried out anyway.” In this way the company lost no production time.
Stress-free production after the refitting
The refitting was planned very carefully and in great detail, and the Glass Solutions teams worked together closely. The start-up was problem-free. The team in Emmen achieved the goals that had been set within just a few days.
The record in the cutting area is now 124 jumbo sheets per shift. The fine-tuning by the Lisec experts was an important phase. Kanne: “The fine-tuning was exciting and very interesting. 2 seconds here, 4 seconds there – it’s fascinating what this achieved.”
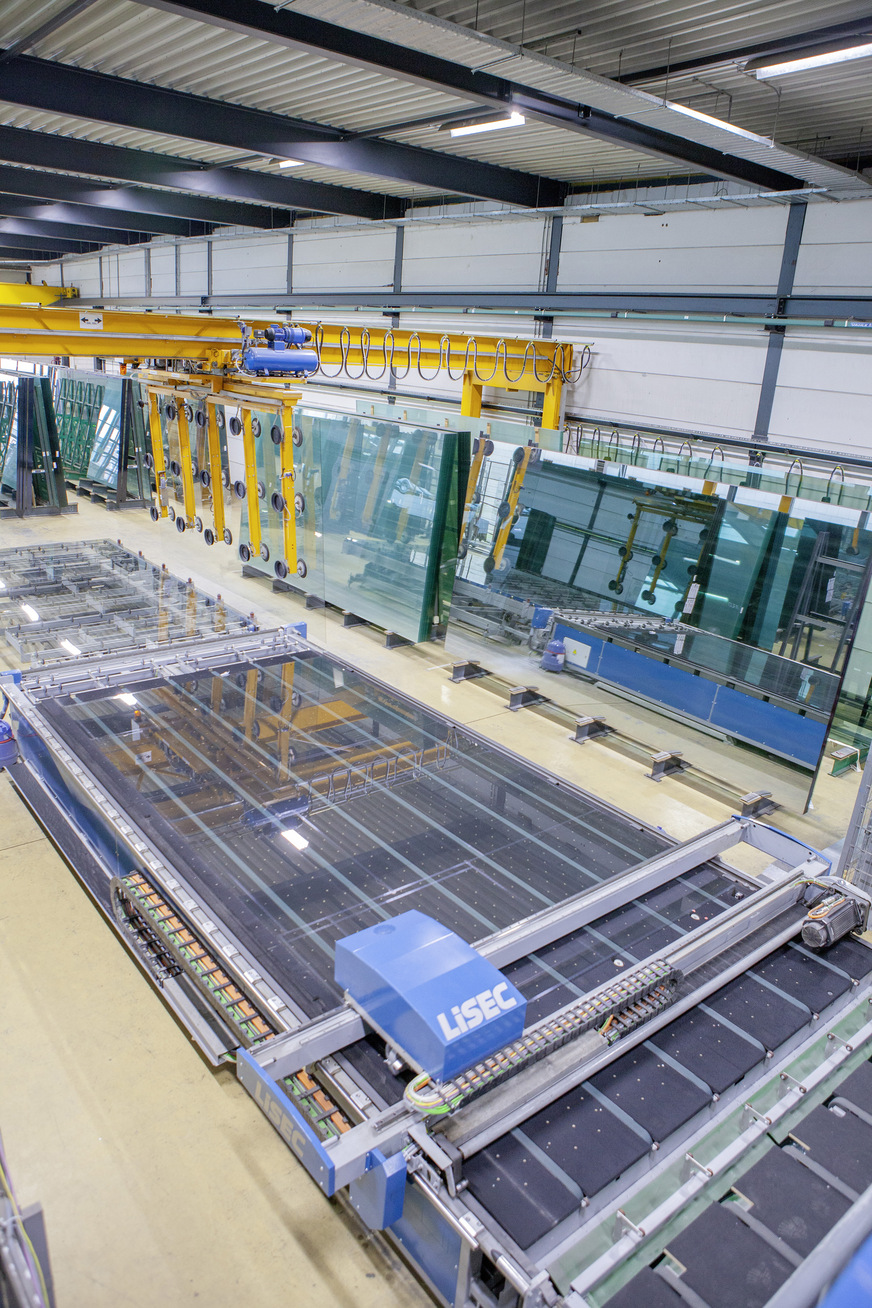
LiSEC
Kanne went on to say that “the system is now more stable than before, and there are fewer faults. We have also become more flexible and are now able to deploy employees in multiple locations.” Incidentally, the modification has also had an impact on the induction of new employees: The operating interfaces are now state of the art, meaning that younger employees in particular find their way around faster.
Support gets more important
The modernisation of the cutting line has also changed the importance of Lisec support. Following the refit, remote support is now possible without restrictions. Herman Kanne: “It is difficult to find technically experienced employees. We now happily rely on the knowledge and experience of Lisec in the area of support. I think that it is important for a supplier to offer this, because it gives us a sense of security.”