Due to the physical requirements involved, heating up the film is the part of this process that takes the longest. New laser separation technology now offers the potential to significantly shorten the processing cycle and improve edge quality.
’The ProLam LSR is equipped with the new heating technology and enables twenty percent more productivity,’ reported Hegla Managing Director Bernhard Hötger. After trying out a number of test setups and systems, the system has now been integrated into the ProLam as an optional extra. The heart of the system is a newly developed laser diode heating unit whose powerful, even, and highly focused laser beam applies heat to the cut contour with a high level of precision. The concentrated energy warms up the film faster, thus speeding up the process of cutting laminated glass. The fact that the diode array is fitted in a fixed position above the glass also helps to save time, as it allows operators to carry out multiple process steps simultaneously based on the appropriate working distance.
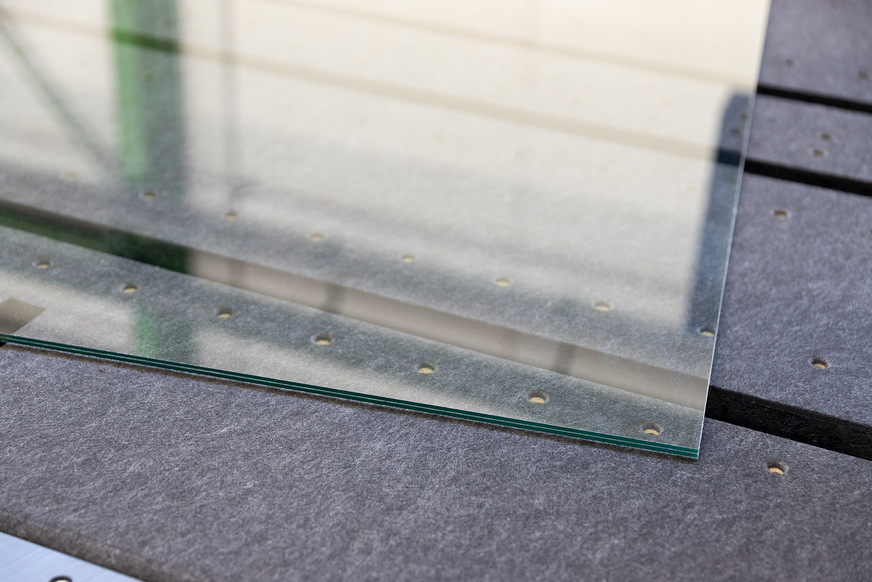
Hegla
Cold edges for higher quality
In addition to reduced cycle times, the process offers advantages in terms of the quality of the cut end product. The heat dissipation from heating lamps always heats up the cut itself and also the area around it. With the new laser technology, however, the surrounding area remains almost completely cold. ’This effect produces the perfect conditions for optimum edge quality,’ Hegla Managing Director Heinrich Ostendarp explained. ’When the glass is pulled apart, only the heated foil around the cut is stretched out – the rest of the pane laminate is unaffected.’ This systematic improvement counters downstream delamination and visible blurring around the edges.
A powerful tool for LSGs with thick films
The laser cutting system’s high productivity is also visible when cutting thicker glass laminates, such as four or eight-ply films. Since the laser beam is concentrated and does not weaken as much when it penetrates the film, the heating time is reduced, producing glass edges of the highest quality.
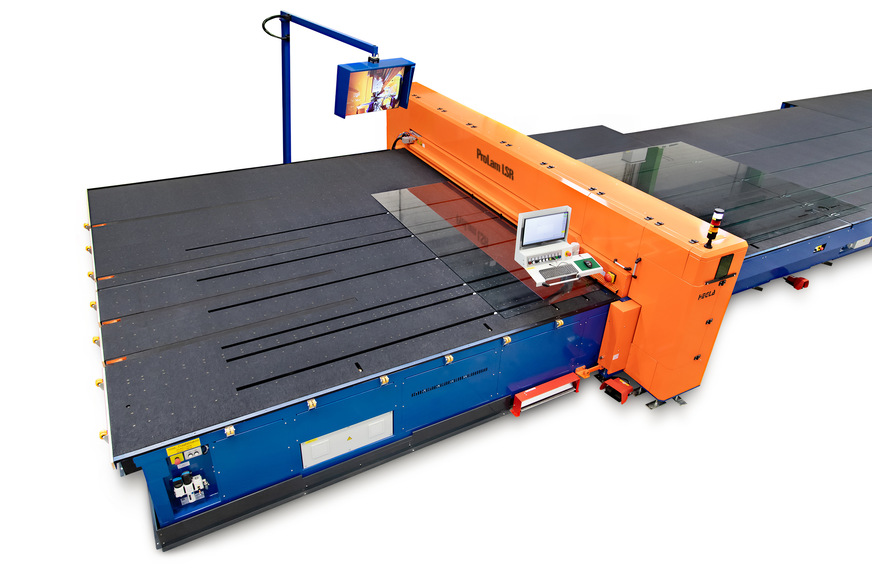
Hegla
Another upside of the new technology is the reduced energy consumption it offers. The laser diode heating unit is split into two parts, so it can be activated in either half-length or full-length mode depending on the size of the glass. The shorter boot-up time and the way the system concentrates the heat also have a positive effect. Likewise, the service life of the laser separation technology also promises to reduce the time spent on maintenance. The laser diodes will perform consistently for 15 years or more in two-shift operation – several times longer than the service life of a conventional heating tube. The newly developed heating technology will soon be available as an option for all ProLam and AdvaLam LSG cutting systems, and can also be retrofitted to new systems.
See also this article: Laser measurement of IGUs with a more practical device
The laser diode heating unit is the product of many years of research conducted by the Hegla Group. The idea of developing the laser diode heating unit is based on a concept by the laser specialists Hegla boraident and Hegla, and eventually came to market in partnership with Jenoptik.
Did you know about the GW News newsletter?