Softsolution and Glaston will be joining forces as partners in the future. The partnership aims to advance the quality measurement of toughened glass to help processors successfully improve their processes. By combining the expertise of the two companies, the performance limits of the toughening process and quality measurement will be further extended.
"When we thought about a partnership between our companies, we immediately realised that both companies are particularly focused on advancing boundaries," says Peter Pfannenstill Sales Director of Softsolution (www.glass-iq.com).
A fully integrated solution and thus a closed loop from the control of a furnace to automated quality feedback will be the key to future challenges and achievements. By combining know-how and experience, the cooperation is aimed at providing the best and most efficient setup for high-quality, heat-treated glass, according to Softsolution and Glaston officials (www.glaston.net).
See also this article: An innovative way to cut tempered safety glass
The first joint project is mainly concerned with anisotropy testing. As quality measurement continues to evolve, the integration of measurement data into the tempering process is becoming increasingly important. With Glaston's "Insight Service Platform", the measurement data can be collected and used as part of the R&D and tempering furnace automation.
What challenges will suppliers of tempering systems face in the future?
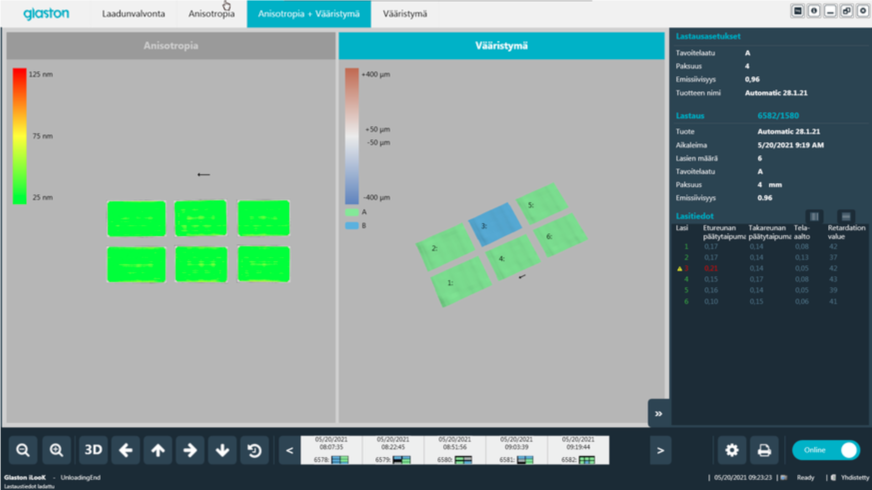
Glaston/Softsolution
The higher degree of automation of tempering lines requires automated quality measurement at more and more positions on the production lines. The demand for quality measurement systems is growing rapidly - and with it the number of defects that such systems must be able to detect. At the same time, tolerances in manufacturing are becoming tighter and tighter for processing companies.
Softsolution and Glaston's first project focuses primarily on anisotropy measurement after the hardening process. Glaston will use the anisotropy measurement technology of the Softsolution LineScanner as part of its iLooK quality measurement products in the future. If technology development proceeds as planned, Glaston will use jointly developed technologies as part of the iLooK product range.
Also interesting: CareyGlass buys Glaston‘s 2,500th glass lifting machine
The close cooperation with machine manufacturers such as Glaston and the resulting challenging research projects are constant innovation drivers for Softsolution, according to the company. The exchange with the global players also enables promising synergies on both sides.
About Glaston
With over 50 years of experience, Glaston is a technology leader in glass processing, providing machines, services and solutions to the architectural, automotive, solar and household appliance industries. The company also supports the development of new technologies that integrate intelligence into glass. Glaston operates globally with manufacturing, service and sales offices in 10 countries.
Glaston's broad product portfolio includes tempered and insulating glass technologies as well as automotive and display glass technologies.
Glaston's IoT solution, the cloud services-based "Insight service platform", is currently used by around 200 toughening plants. The service will be expanded to cover laminating and insulating glass manufacturing as well.
About Softsolution
Softsolution develops and manufactures automated quality assurance systems, including scanners, for the glass industry. For more than 20 years, the Austrian company has been offering high-performance technologies that have impressed a large number of customers, especially in glass processing industries, with their stability, operational reliability and performance.
Currently, more than 1100 systems are in use worldwide. A large network of partners makes scanning systems for the flat glass industry, produced in Waidhofen/Ybbs (Austria), which are available all over the world.