For some time now, the development of laser processing of glass has focused on cutting and drilling by perforation. In the early days of laser cutting glass, tension-induced processes were used, and the “perforation” process became increasingly popular.
Thanks to the availability of lasers with ultra-short pulses, so either nanoseconds (a billionth of a second) or femtoseconds (a trillionth of a second) pulses that are shot at the glass, another way of processing glass is now opening up. The unimaginably short laser pulses create a kind of small channel in the glass.
If you now place one of these small channels on the other, there is a continuous stretch of separation points in the glass – the perforation is complete. A glass laser-cut in this way either separates solely by this treatment or can be separated using a low voltage or by thermal or mechanical means. To increase the speed, there are developments that do not only use a single laser beam, but an entire bundle of such beams that work in parallel. Using an ultra-short pulse laser, glass can not only be cut, but also drilled and milled.
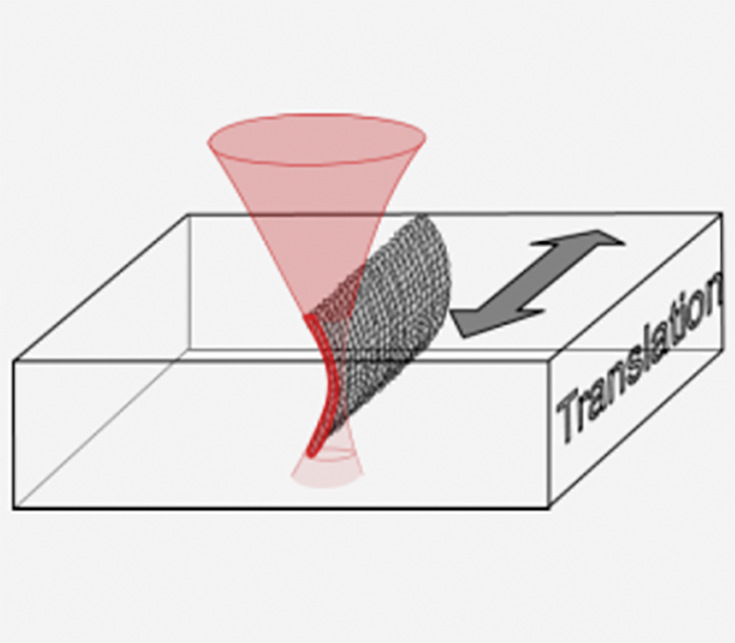
Trumpf Laser and System Technology
The further development of the beam sources has reduced the price, so that today ultra-short pulse lasers are available to glass refiners at acceptable prices.
Practical applications of lasers
Dr. Thoma Rainer from Hegla boraident presented a range of products that can be manufactured with Laserbird, the in-house laser processing system. The main thing here is to change the surface of the glass, but cutting or drilling is also possible.
The range of products that can be achieved ranges from decoating in the edge area (insulating glass production), heatable glass, bird protection glass, radar glass, glass that improves cell phone reception, sun protection structures to functional imprints for generating an alarm glass. In addition, glasses can be provided with a laser marking to track the glass through production (automated production).
Counterfeit-proof product marking on glass was the topic of Kay Bischoff from the Laserzentrum Hannover (LHZ). Increasingly, there is a requirement for high-quality glass products to be able to differentiate them from counterfeits and also to give the customer the assurance that they have bought the original.
The glass working group at the LZH deals with microstructures that are introduced into glass and produce a hologram there; this then creates a clear identification.
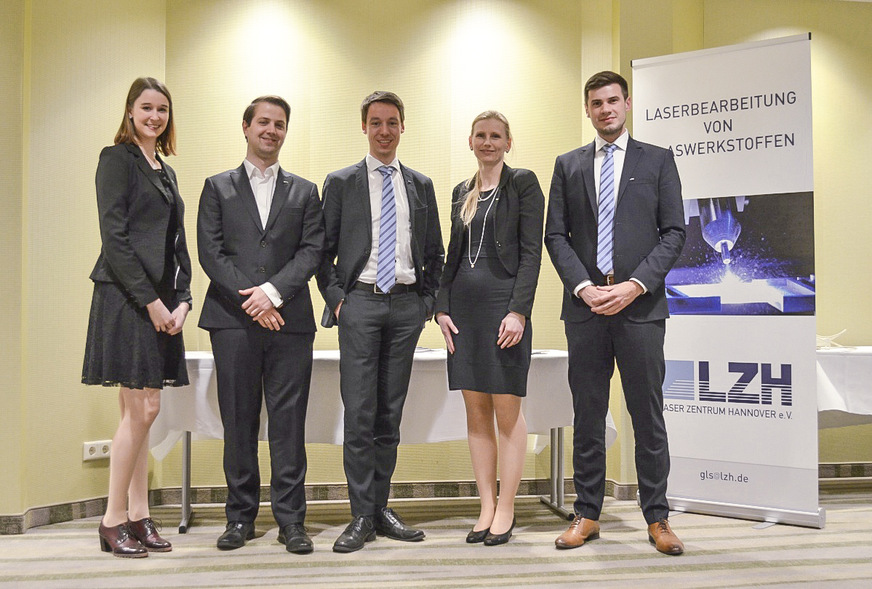
LZH
Laser polishing is a process that removes the smallest unevenness on the glass surface with the help of the energy supplied by the laser. This process is used, for example, with glass lenses that are difficult to process with other processes due to their curved surface.
Using lasers for tracking glass
Other fields of glass processing that were presented were inverse processing for microstructure technology (such as analysis of small quantities in medical technology), welding of (quartz) glasses and the emerging 3-D printing. However, this procedure is still in laboratory status.
Dr. Schäfer from the Trumpf company gave an extremely interesting outlook into the future. In the first works it was possible to have the laser cut 'around corners'. Again, an ultrashort pulse laser and the perforation process described above are used. In the not too distant future, this could generate a C-edge for flat glass panes, which would combine the advantages of classic design with the process advantages of laser technology. So it will be interesting to see how the development will continue in the future.
Guest author: Thomas Schmidt, glass consultant